Gunning material and gunning method for RH dip pipe
A dipping tube and gunning material technology, which is applied in the direction of manufacturing tools, casting molten material containers, casting equipment, etc., can solve the problems of low production efficiency, long time, poor gunning efficiency, etc., to improve adhesion rate, reduce dosage, The effect of ensuring quality
- Summary
- Abstract
- Description
- Claims
- Application Information
AI Technical Summary
Problems solved by technology
Method used
Image
Examples
Embodiment 1
[0037] A RH dip tube gunning method provided in this embodiment is produced on a non-oriented silicon steel production line in a steel factory, and its RH gunning process is as follows:
[0038] After the RH treatment is completed, the empty space is broken, and the ladle is lowered to 20cm directly below the dipping tube, and it stays for 0.5min. When about 35% of the molten steel remains in the vacuum tank and the temperature of the outer wall of the RH dipping tube is 1277°C, the ladle is lowered and transported out; the gunning car starts To the working position below the RH dipping tube, the inner and outer spray guns are raised to the initial processing position by the lifting motor, and the two spray guns of the gunning machine are used to simultaneously spray and maintain the outer and inner walls of the RH dipping tube. When the gunning starts, the temperature of the outer wall of the RH dipping tube is 1192 ℃, at this time, the water distribution rate of the external ...
Embodiment 2
[0041] A RH dip tube gunning method provided in this embodiment is produced on a cold-rolled substrate production line of a steel factory, and the RH gunning process operation process is as follows:
[0042] After the RH treatment is finished, the ladle is lowered to 50cm below the dipping tube and stays for 1.5min. After the residual molten steel in the vacuum tank flows out, when the temperature of the outer wall of the RH dipping tube is 1299°C, the ladle is lowered and transported out; the gunning vehicle drives to the RH At the working position below the dipping tube, the inner and outer spray guns are lifted to the initial processing position by the lifting motor, and the two spray guns of the gunning machine are used to simultaneously repair and maintain the inner and outer walls of the RH dipping tube. The water distribution rate of the spray gun is 5%, the feeding speed is 40kg / min, the rotation speed of the spray gun itself is 5r / min, the revolution speed is 10r / min, ...
Embodiment 3
[0046] A kind of RH dip tube gunning method provided in this embodiment is produced on the automobile plate production line of a certain steel factory, and its RH gunning process operation process is as follows:
[0047] After the RH treatment is finished, the ladle is lowered to 38cm below the dipping tube and stays for 1.0min. After the residual molten steel in the vacuum tank flows out and the temperature of the outer wall of the RH dipping tube reaches 1250°C, the ladle is lowered and transported out; the gunning vehicle drives to the RH At the working position below the dipping tube, the inner and outer spray guns are raised to the initial processing position by the lifting motor, and the two spray guns of the gunning machine are used to simultaneously repair and maintain the inner and outer walls of the two RH dipping tubes. When the gunning starts, the temperature of the outer wall of the RH dipping tube is 1192°C , at this time, the water distribution rate of the spray ...
PUM
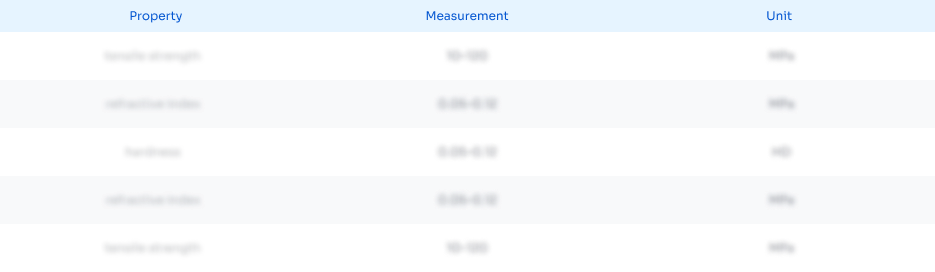
Abstract
Description
Claims
Application Information

- R&D
- Intellectual Property
- Life Sciences
- Materials
- Tech Scout
- Unparalleled Data Quality
- Higher Quality Content
- 60% Fewer Hallucinations
Browse by: Latest US Patents, China's latest patents, Technical Efficacy Thesaurus, Application Domain, Technology Topic, Popular Technical Reports.
© 2025 PatSnap. All rights reserved.Legal|Privacy policy|Modern Slavery Act Transparency Statement|Sitemap|About US| Contact US: help@patsnap.com