Preparation method of bismuth oxychloride graphite composite electrode material
A technology of bismuth oxychloride and composite electrode is applied in chemical instruments and methods, separation methods, water/sludge/sewage treatment and other directions, which can solve the problems of difficult removal and great harm, achieve low cost, reduce operating energy consumption, The effect of enhancing the speed of electron transfer
- Summary
- Abstract
- Description
- Claims
- Application Information
AI Technical Summary
Problems solved by technology
Method used
Image
Examples
Embodiment 1
[0032] as attached figure 1 Shown, a kind of preparation method of bismuth oxychloride graphite composite electrode material, concrete steps are:
[0033] (1) Get a cleaned Gp graphite plate (50mm * 50mm, 60mm * 80mm, 1mm) and etch it in 50ml 10% dilute nitric acid solution for 8 hours under the condition of heating in a water bath at 80°C;
[0034] (2) The above-mentioned etched graphite plate is cleaned in ethanol and deionized water, and put into a drying oven to dry for 3 hours at 40° C. for subsequent use;
[0035] (3) Dissolve 0.24g Bi(NO3) 3 5H2O and 0.04g KCl and 0.01g dispersant (hexadecyltrimethylammonium bromide) in 20ml ethylene glycol at room temperature, and fully stir , moved into a sealed container as a bismuth oxychloride loading agent;
[0036] (4) Put the above-mentioned dried graphite plate into the 50ml Teflon liner of the autoclave, and move the spare bismuth oxychloride loading agent into the autoclave, after the autoclave is sealed, place it in the dr...
Embodiment 2
[0041] as attached figure 1 Shown, a kind of preparation method of bismuth oxychloride graphite composite electrode material, concrete steps are:
[0042] (1) Get a cleaned Gp graphite plate (50mm * 50mm, 60mm * 80mm, 1mm) and etch it in 50ml 20% dilute nitric acid solution for 8 hours under the condition of heating in a water bath at 100°C;
[0043] (2) The above-mentioned etched graphite plate is cleaned in ethanol and deionized water, and put into a drying oven to dry for 3 hours at 40° C. for subsequent use;
[0044] (3) Dissolve 0.24g Bi(NO3)3 5H2O, 0.04g KCl and 0.01g dispersant (polyvinylpyrrolidone) in 20ml ethylene glycol at room temperature, stir well, and transfer to a sealed container for use as Bismuth oxychloride loading agent;
[0045] (4) Put the above-mentioned dried graphite plate into the 50ml Teflon liner of the autoclave, and move the spare bismuth oxychloride loading agent into the autoclave, after the autoclave is sealed, place it in the drying box He...
PUM
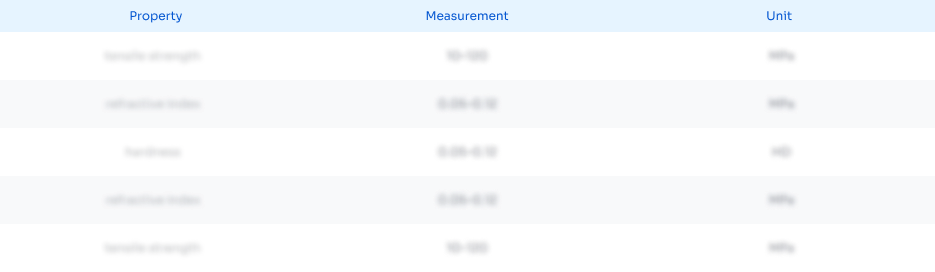
Abstract
Description
Claims
Application Information

- R&D
- Intellectual Property
- Life Sciences
- Materials
- Tech Scout
- Unparalleled Data Quality
- Higher Quality Content
- 60% Fewer Hallucinations
Browse by: Latest US Patents, China's latest patents, Technical Efficacy Thesaurus, Application Domain, Technology Topic, Popular Technical Reports.
© 2025 PatSnap. All rights reserved.Legal|Privacy policy|Modern Slavery Act Transparency Statement|Sitemap|About US| Contact US: help@patsnap.com