Combined technology for milling and grinding tooth parts of spiral taper gear
A technology of spiral bevel gear and combined process, which is applied in the direction of manufacturing tools, heat treatment equipment, furnaces, etc., can solve the problems that the tooth surface error cannot be completely eliminated, the heat treatment deformation error, the one-time investment of equipment is large, and the adjustment of machine tools is complicated, so as to reduce equipment Effects of investment, improvement of production efficiency, and simplified process flow
- Summary
- Abstract
- Description
- Claims
- Application Information
AI Technical Summary
Problems solved by technology
Method used
Examples
Embodiment Construction
[0013] Process of the present invention is described in detail below:
[0014] For a driven wheel with a diameter of φ450mm and a number of teeth of 43 teeth, the process is: forging billet: outer diameter φ460mm, inner hole φ220mm, thickness 71mm—pre-heat treatment, normalizing: temperature 920-950°C, time 2-2.5 hours, surface The hardness is 156~207HBS—car blank—milling teeth—chamfering, cleaning—heat treatment: carburizing and quenching temperature is 20-24 hours, of which the carburizing temperature is 920-930°C, and the diffusion temperature is 920-930°C , the holding temperature is 830-850°C, the quenching temperature is 830-850°C, the effective hardened layer depth is 1.7-2.1mm, the surface hardness is 58-63HRC, the core hardness is 33-45HRC, retained austenite, martensite, carbonization Grades 1 to 4, surface non-martensitic depth less than 0.02mm, - fine grinding inner hole and positioning end face - grinding bruises, surface roughness of grinding teeth is Ra0.8.
[...
PUM
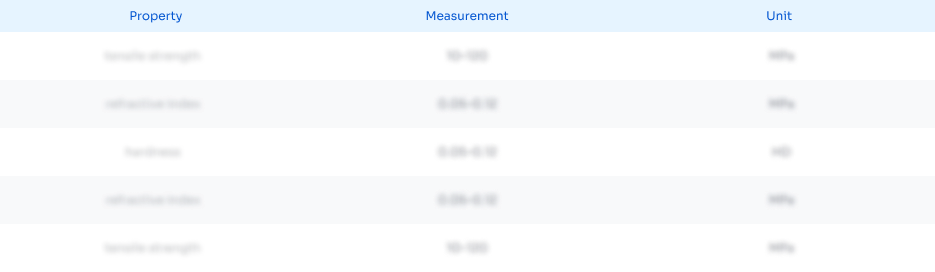
Abstract
Description
Claims
Application Information

- R&D
- Intellectual Property
- Life Sciences
- Materials
- Tech Scout
- Unparalleled Data Quality
- Higher Quality Content
- 60% Fewer Hallucinations
Browse by: Latest US Patents, China's latest patents, Technical Efficacy Thesaurus, Application Domain, Technology Topic, Popular Technical Reports.
© 2025 PatSnap. All rights reserved.Legal|Privacy policy|Modern Slavery Act Transparency Statement|Sitemap|About US| Contact US: help@patsnap.com