Waste gas reduction and harmlessness treatment method in waste lithium battery recycling process
A waste lithium battery and treatment method technology, which is applied in the field of waste gas treatment in the lithium battery recycling process, can solve the problems of large natural gas consumption, achieve the effects of reducing oxygen costs, better absorption effect, and realization of recycling
- Summary
- Abstract
- Description
- Claims
- Application Information
AI Technical Summary
Problems solved by technology
Method used
Image
Examples
Embodiment 1
[0025] The 10,000 t / a waste lithium iron phosphate battery production line is crushed under the condition of airtight and nitrogen protection, low-temperature volatilization at 100°C for 1 hour, high-temperature pyrolysis at 550°C for 1 hour, and the amount of tail gas produced is 800m 3 / h, the exhaust gas contains organic components such as electrolyte, pyrolysis gas, and protective gas nitrogen and dioxin. After the waste gas is collected, it is incinerated by oxygen enrichment, the incineration temperature is 1100°C, and the incineration time is 3s. After incineration, part of the heat is recovered through a heat exchanger, and then quenched by water spraying. The spray tower adopts a graphite tower, and the spraying water volume is 1t / h. The residence time of the exhaust gas in the quenching tower is 2s, and the exhaust gas temperature after quenching is below 200°C. The exhaust gas after quenching is sprayed into activated carbon to absorb solid powder such as dust and d...
Embodiment 2
[0027] 10,000 t / a waste ternary battery production line, under the condition of airtight and nitrogen protection, crushing, low-temperature volatilization at 100°C for 1 hour, high-temperature pyrolysis at 550°C for 1 hour, and the amount of exhaust gas produced is 800m 3 / h, the exhaust gas contains organic components such as electrolyte, pyrolysis gas, and protective gas nitrogen and dioxin. The waste gas treatment process is carried out according to Example 1. The voc content in exhaust gas is 9mg / m 3 , HF content 6mg / m 3 , dust content 15mg / m 3 , dioxin content 0.3ng TEQ / Nm 3 .
Embodiment 3
[0029] The 10,000 t / a waste lithium iron phosphate battery production line is crushed under the condition of airtight and nitrogen protection, and high-temperature pyrolysis is carried out at 550°C for 1 hour, and the exhaust gas produced is 500m 3 / h, the exhaust gas contains organic components such as electrolyte, pyrolysis gas, and protective gas nitrogen and dioxin. The waste gas treatment process is carried out according to Example 1. The voc content in exhaust gas is 10mg / m3 3 , HF content 6mg / m 3 , dust content 10mg / m 3 , dioxin content 0.3ng TEQ / Nm 3 .
PUM
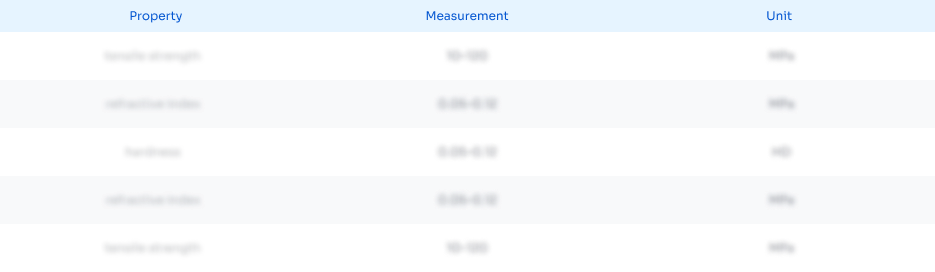
Abstract
Description
Claims
Application Information

- R&D Engineer
- R&D Manager
- IP Professional
- Industry Leading Data Capabilities
- Powerful AI technology
- Patent DNA Extraction
Browse by: Latest US Patents, China's latest patents, Technical Efficacy Thesaurus, Application Domain, Technology Topic.
© 2024 PatSnap. All rights reserved.Legal|Privacy policy|Modern Slavery Act Transparency Statement|Sitemap