Preparation method of iron-carbon micro-electrolysis filler for retarding formation of isolating layer through rare earth carbonization
A technology of iron-carbon micro-electrolysis and rare earth carbonization, which is applied in chemical instruments and methods, water/sewage treatment, water/sludge/sewage treatment, etc. Inconvenient to deal with, fast formation of the isolation layer, etc., to achieve the effect of enhancing electrolytic conductivity, improving porous firmness, and improving electrolytic efficiency
- Summary
- Abstract
- Description
- Claims
- Application Information
AI Technical Summary
Problems solved by technology
Method used
Examples
Embodiment 1
[0023] like figure 1 Shown, a kind of rare earth carbonization slows down the preparation method of the iron-carbon micro-electrolytic filler that isolation layer forms, comprises the steps:
[0024] Step 1. Get 50-90g of Fe, 5-20g of C, 1-2g of yttrium, 1-2g of cerium and 1.5-3g of tungsten from each storage container and mix them evenly into a refractory container. Put it into a sintering furnace and sinter for 16 hours according to three temperature stages of 1200-1250°C, 1300-1350°C and 1400-1450°C, so that the above materials are integrated and solid-phase combined;
[0025] Step 2. Grinding the mixed metal lumps: the cooled mixed metal lumps are crushed by a crusher, and then ground to nano-level mixed metal powders with a total mass of 100-200 g, and stored for later use.
[0026] Further, in the step 1, 5-10g of Ti, 10-20g of Ag, 2g of cerium and 3g of tungsten are mixed together to form a cerium-tungsten electrode.
[0027] The preparation method of the iron-carbon ...
Embodiment 2
[0029] like figure 1 Shown, a kind of rare earth carbonization slows down the preparation method of the iron-carbon micro-electrolytic filler that isolation layer forms, comprises the steps:
[0030] Step 3. Paste preparation: Weigh graphene powder, ytterbium powder, scandium chloride powder, and viscous agent according to the ratio of 8:1:2:12 or 10:1:1:6 and put them into the mixer The silo is fully mixed by the mixer to form a paste mixture, which is ready for use;
[0031] Step 4, Slurry carbonization: Take 100g of mixed metal powder from step 2 and put it into the silo of the mixer equipped with paste-like mixed liquid in step 3 and mix well until the surface of each fine mixed metal powder particle is fully slurryed. After entering the dryer, it is dried at a gradual high temperature of 150-300°C. After cooling and taking it out, it is put into a refractory container and placed in a high-temperature sintering furnace, so that the surface of the mixed metal powder is car...
Embodiment 3
[0036] like figure 1 Shown, a kind of rare earth carbonization slows down the preparation method of the iron-carbon micro-electrolytic filler that isolation layer forms, comprises the steps:
[0037]Step 5. Pill making: Take any one of the 20-90 parts of mixed metal powder in step 4 and add an appropriate amount of coupling agent, and the mass of each carbonized mixed metal powder is 2-3 grams, and send it into a mixer for full stirring Mix for 15-25 minutes, add 0.2-0.5g of natural rubber juice evenly, stir and react for 30-45 minutes, it is in a paste state, then pour it into a pelletizing mold and send it to a microwave oven at 260-960°C for drying and sintering for 10- After 12 hours, it was cooled to below 30°C and released from the furnace to obtain an iron-carbon micro-electrolytic filler formed by a rare earth carbonization slowing isolation layer.
[0038] The preparation method of the iron-carbon micro-electrolytic filler formed by the above-mentioned rare earth car...
PUM
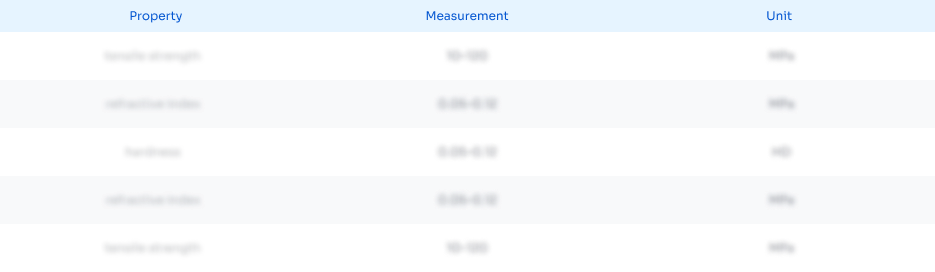
Abstract
Description
Claims
Application Information

- R&D
- Intellectual Property
- Life Sciences
- Materials
- Tech Scout
- Unparalleled Data Quality
- Higher Quality Content
- 60% Fewer Hallucinations
Browse by: Latest US Patents, China's latest patents, Technical Efficacy Thesaurus, Application Domain, Technology Topic, Popular Technical Reports.
© 2025 PatSnap. All rights reserved.Legal|Privacy policy|Modern Slavery Act Transparency Statement|Sitemap|About US| Contact US: help@patsnap.com