Method for manufacturing high-speed steel roller
A high-speed steel and roll technology, applied in the field of high-speed steel roll production, can solve problems such as block-off processing efficiency and easy chipping, and achieve the effects of solving processing difficulties, improving processing efficiency, and high processing efficiency
- Summary
- Abstract
- Description
- Claims
- Application Information
AI Technical Summary
Problems solved by technology
Method used
Image
Examples
Embodiment 1
[0065] A method for making a high-speed steel roll, the high-speed steel roll comprises an outer layer and an inner core, and the chemical composition of the outer layer is calculated by weight percentage: C1.2%, Si0.5%, Mn0.5%, P0. 030%, S0.032%, Cr1.0%, Ni3.0%, Mo1.0% and V4.0%, the balance is Fe; the chemical composition of the inner core layer is calculated by weight percentage: C3.1%, Si1.0%, Mn1.1%, P0.031%, S0.014%, Cr0.12%, Ni0.5% and Mg0.04%, the balance is Fe;
[0066] Described manufacturing method comprises the steps:
[0067] (1) Modeling work:
[0068] Prepare the metal casting mold, casting end cover, upper box and bottom box, respectively smooth and smooth, check whether the end cover is intact, add the end cover ingredients, steel brick particles, repair package binding material, bentonite and carbon powder, use semi-steel The coating is dust-pressed on the casting mold end cover, upper box and bottom box, and a layer of lead powder paint is applied after dr...
Embodiment 2
[0083]A method for making a high-speed steel roll, the high-speed steel roll comprises an outer layer and an inner core, and the chemical composition of the outer layer is calculated by weight percentage: C1.4%, Si0.6%, Mn1.0%, P0. 080%, S0.080%, Cr2.1%, Ni4.1%, Mo1.5% and V4.5%, the balance is Fe; the chemical composition of the inner core layer is calculated by weight percentage: C3.5%, Si1.5%, Mn1.8%, P0.080%, S0.080%, Cr0.15%, Ni0.7% and Mg0.051%, the balance is Fe;
[0084] Described manufacturing method comprises the steps:
[0085] (1) Modeling work:
[0086] Prepare the metal casting mold, casting end cover, upper box and bottom box, respectively smooth and smooth, check whether the end cover is intact, add the end cover ingredients, steel brick particles, repair package binding material, bentonite and carbon powder, use semi-steel The coating is dust-pressed on the casting mold end cover, upper box and bottom box, and a layer of lead powder paint is applied after dr...
Embodiment 3
[0101] A method for making a high-speed steel roll, the high-speed steel roll comprises an outer layer and an inner core, and the chemical composition of the outer layer is calculated by weight percentage: C1.34%, Si0.57%, Mn0.65%, P0. 036%, S0.032%, Cr1.10%, Ni3.10%, Mo1.19% and V4.43%, the balance is Fe; the chemical composition of the inner core layer is calculated by weight percentage: C3.19%, Si1.44%, Mn1.44%, P0.031%, S0.014%, Cr0.14%, Ni0.59% and Mg0.050%, the balance is Fe;
[0102] Described manufacturing method comprises the steps:
[0103] (1) Modeling work:
[0104] Prepare the metal casting mold, casting end cover, upper box and bottom box, respectively smooth and smooth, check whether the end cover is intact, add the end cover ingredients, steel brick particles, repair package binding material, bentonite and carbon powder, use semi-steel The coating is dust-pressed on the casting mold end cover, upper box and bottom box, and a layer of lead powder paint is appl...
PUM
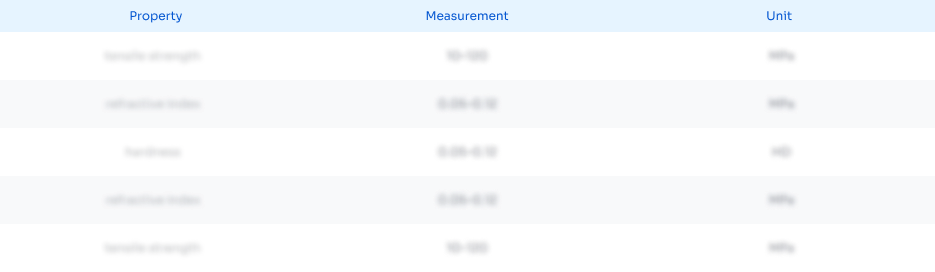
Abstract
Description
Claims
Application Information

- R&D Engineer
- R&D Manager
- IP Professional
- Industry Leading Data Capabilities
- Powerful AI technology
- Patent DNA Extraction
Browse by: Latest US Patents, China's latest patents, Technical Efficacy Thesaurus, Application Domain, Technology Topic, Popular Technical Reports.
© 2024 PatSnap. All rights reserved.Legal|Privacy policy|Modern Slavery Act Transparency Statement|Sitemap|About US| Contact US: help@patsnap.com