Catalyst for synergistically controlling nitrogen oxides and particulate matters in diesel engine tail gas as well as preparation method and application thereof
A nitrogen oxide, synergistic control technology, applied in metal/metal oxide/metal hydroxide catalysts, chemical instruments and methods, physical/chemical process catalysts, etc., can solve the problems of poor selectivity and high ignition temperature, and achieve High active loading, simple and controllable preparation, and good synergistic removal efficiency
- Summary
- Abstract
- Description
- Claims
- Application Information
AI Technical Summary
Problems solved by technology
Method used
Image
Examples
Embodiment 1
[0027] A method for preparing a catalyst for synergistic control of nitrogen oxides and particulate matter in diesel engine exhaust, the specific preparation steps of which are as follows:
[0028] Step S1, use deionized water to wash and dry the honeycomb ceramics with a size of 100mm×100mm×50mm, then immerse them in alumina sol with a mass fraction of 20%, and let them stand for 30 minutes. Take out the alumina sol, use a high-pressure air gun to blow out the residual alumina sol in the pores of the honeycomb ceramics, dry the honeycomb ceramics in an oven at 100°C, transfer them to a muffle furnace, and bake them at 500°C for 4 hours to prepare Obtain catalyst carrier A;
[0029] Step S2, add the accurately weighed precursor salt of the metal active component, including: 316g of copper nitrate, 293g of manganese acetate and 262g of cerium nitrate, into 4L of deionized water, stir until it is uniformly dissolved, measure 4L of alumina sol, Add it into the solution and stir ...
Embodiment 2
[0035] Step S1, use deionized water to wash and dry the honeycomb ceramics with a size of 100mm×100mm×50mm, then immerse them in alumina sol with a mass fraction of 20%, and let them stand for 30 minutes. Take out the alumina sol, use a high-pressure air gun to blow out the residual alumina sol in the pores of the honeycomb ceramics, dry the honeycomb ceramics in an oven at 100°C, transfer them to a muffle furnace, and bake them at 500°C for 4 hours to prepare Obtain catalyst carrier A;
[0036] Step S2, add the precursor salt of the metal active component accurately weighed, including: 316g copper nitrate, 293g manganese acetate and 262g cerium nitrate, 15g palladium chloride, into 4L deionized water, stir until it dissolves evenly, measure 4L of alumina sol was added to the solution and stirred until uniform, and the active component sol B was prepared;
[0037]Step S3, immerse the catalyst carrier A obtained by roasting in step S1 in the active component sol B in the step ...
Embodiment 3
[0041] Step S1, use deionized water to wash and dry the honeycomb ceramics with a size of 100mm×100mm×50mm, then immerse them in a silica sol with a mass fraction of 30%, and let them stand for 30 minutes to remove the honeycomb ceramics from Take out the alumina sol, use a high-pressure air gun to blow out the residual alumina sol in the pores of the honeycomb ceramics, dry the honeycomb ceramics in an oven at 100°C, transfer them to a muffle furnace, and bake them at 500°C for 4 hours to prepare Obtain catalyst carrier A;
[0042] Step S2, add the precursor salt of the metal active component accurately weighed, including: 437g copper nitrate, 406g manganese acetate and 363g cerium nitrate, into 4L deionized water, stir until it dissolves evenly, measure 4L silica sol and 10 mL of nitric acid solution with a concentration of 2 mol / L was added to the solution and stirred until uniform to prepare the active component sol B;
[0043] Step S3, immerse the catalyst carrier A obta...
PUM
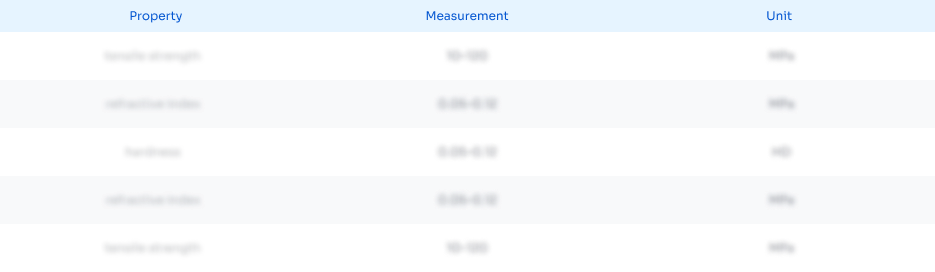
Abstract
Description
Claims
Application Information

- R&D
- Intellectual Property
- Life Sciences
- Materials
- Tech Scout
- Unparalleled Data Quality
- Higher Quality Content
- 60% Fewer Hallucinations
Browse by: Latest US Patents, China's latest patents, Technical Efficacy Thesaurus, Application Domain, Technology Topic, Popular Technical Reports.
© 2025 PatSnap. All rights reserved.Legal|Privacy policy|Modern Slavery Act Transparency Statement|Sitemap|About US| Contact US: help@patsnap.com