Preparation method and application of composite material
A composite material and composite material technology, which is applied in the field of composite material preparation and can solve the problems of electrical conductivity and crystallinity decline.
- Summary
- Abstract
- Description
- Claims
- Application Information
AI Technical Summary
Problems solved by technology
Method used
Image
Examples
Embodiment 1
[0072] This embodiment has prepared a kind of composite material, and specific preparation method is:
[0073] A1. Preparation of nickel mercaptide
[0074] A1a: NiCl 2 ·6H 2 O is dissolved in ethanol, and trimethylammonia is added to the solution to form triethylamine nickel complex, and the molar ratio of divalent nickel salt and trimethylamine is 1:2.
[0075] A1b: Add 2 times the molar mass of n-butanethiol to the complex solution, stir at 70°C for 5 hours to form a precipitate of n-butanethiol nickel, filter the precipitate, and wash it with acetonitrile and methanol for 5 times. The precipitate was dried at 80°C for 10 hours, and the dried nickel n-butanethiol was dissolved in toluene for later use.
[0076] A2. Preparation of composite materials
[0077] A2a: Cut waste polystyrene plastic plates into irregular shapes of 0.4-1.2 cm, wash them with 1mol / L hydrochloric acid at 50°C for 4 hours, filter them, and wash them with deionized water until neutral. The fragmen...
Embodiment 2
[0080] This embodiment has prepared a kind of supercapacitor, and specific preparation method is:
[0081] A2. Supercapacitor
[0082] A2a: Disperse the composite material in Example 1 into an isopropanol solution containing 10% perfluorosulfonic acid, then coat the slurry on a carbon cloth as an electrode, and separate it with a Celgard diaphragm in 3M KOH, thereby Assembled into a double-layer capacitor, the loading of the composite material is 0.4mg / cm 2 .
Embodiment 3
[0084] This embodiment has prepared a kind of composite material, and specific preparation method is:
[0085] A1. Preparation of nickel mercaptide
[0086] A1a: NiCl 2 ·6H 2 O is dissolved in ethanol, and trimethylammonia is added to the solution to form triethylamine nickel complex, and the molar ratio of divalent nickel salt and trimethylamine is 1:2.
[0087] A1b: Add 2 times the molar mass of n-butanethiol to the complex solution, stir at 70°C for 5 hours to form a precipitate of n-butanethiol nickel, filter the precipitate, and wash it with acetonitrile and methanol for 5 times. The precipitate was dried at 80°C for 10 hours, and the dried nickel n-butanethiol was dissolved in toluene for later use.
[0088] A2. Preparation of composite materials
[0089] A2a: Cut waste polystyrene plastic plates into irregular shapes of 0.4 to 1.2 cm, wash them with 1mol / L hydrochloric acid at 50°C for 4 hours, filter them, and wash them with deionized water until neutral. Place in...
PUM
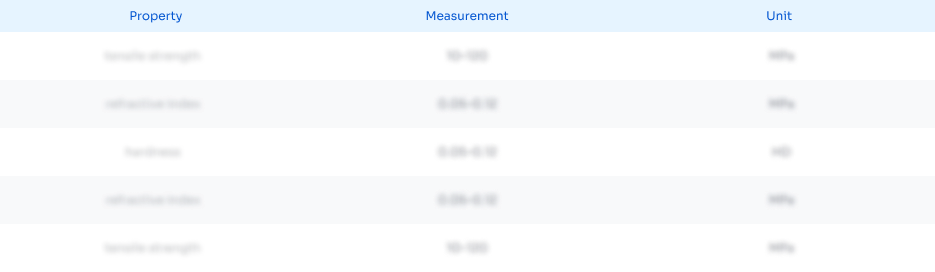
Abstract
Description
Claims
Application Information

- R&D
- Intellectual Property
- Life Sciences
- Materials
- Tech Scout
- Unparalleled Data Quality
- Higher Quality Content
- 60% Fewer Hallucinations
Browse by: Latest US Patents, China's latest patents, Technical Efficacy Thesaurus, Application Domain, Technology Topic, Popular Technical Reports.
© 2025 PatSnap. All rights reserved.Legal|Privacy policy|Modern Slavery Act Transparency Statement|Sitemap|About US| Contact US: help@patsnap.com