Carbon black dispersion, and preparation method and application thereof
A dispersion and carbon black technology, applied in the direction of single-component polyester rayon, dyeing low molecular organic compound treatment, adding pigments in spinning solution, etc., can solve the problem of washing resistance and friction resistance of colored polyester fibers Poor spinnability, poor spinnability of polyester, low fiber coloring strength, etc., to achieve good spinnability, improved stability, and low filter press value
- Summary
- Abstract
- Description
- Claims
- Application Information
AI Technical Summary
Problems solved by technology
Method used
Image
Examples
Embodiment 1
[0038] The surface containing a mass ratio of 1: 0.05 containing a hydroxyl group with a hydroxybenzoic acid, and the addition of 15% N, N-dimethylformamide having a carbon black containing a hydroxyl group containing a hydroxyl group, and is uniformly dispersed. 45min to get modified carbon black;
[0039] The mass is 3 parts of the surfactant A, the mass is 3 parts of the surfactant B1, dispersed into a mass of 74 parts of ethylene glycol, and the mass is 20 parts of modified carbon black, and after mixing, hydrogen The sodium oxide regulates the pH of 8.0, dispersion, ground, filtration, and defoaming to obtain a carbon black dispersion.
Embodiment 2
[0041] The surface containing a mass ratio of 1: 0.06 contains a hydroxybenzoic acid, which is added to the surface containing 10% N, N-dimethylformamide, and the dispersion is uniform, and is kneaded with a kneader. 30min, resulting in modified carbon black;
[0042] The mass is 2 parts of the surfactant A, the mass is 5 parts of the surfactant B2, dispersed into a mass of 63 parts of ethylene glycol, and the mass is 30 parts of modified carbon black, thoroughly mixed, hydrogen The potassium oxide regulates the pH of 7.0, dispersion, ground, filtered, and defoamed to obtain a carbon black dispersion.
Embodiment 3
[0044] The surface containing a mass ratio of 1: 0.07 contains a hydroxyl group with a hydroxyl group, and the surface contains 16% N, N-dimethylformamide, and the dispersion is uniform. Using a kneader for 40 min to obtain modified carbon black.
[0045] The mass is 5 parts of the surfactant A, the mass is 4 parts of the surfactant B3, dispersed into a mass of 51 parts of ethylene glycol, and the mass is 40 parts of modified carbon black and the mass is 0.01 parts. After 2-benzothiazoline-3-ketone, after mixing, the pH is adjusted with a potassium hydroxide having a pH of 9.0, dispersion, ground, filtration, and defoaming to obtain a carbon black dispersion.
PUM
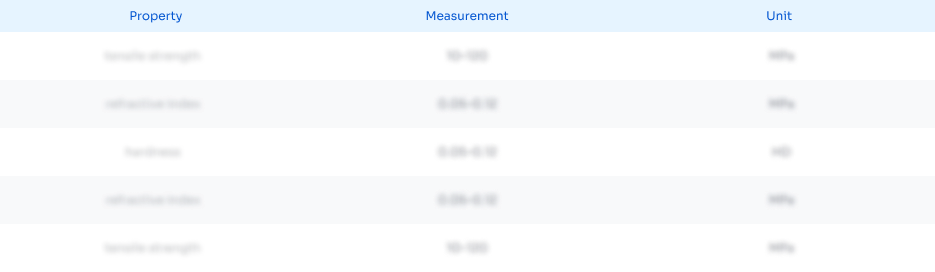
Abstract
Description
Claims
Application Information

- R&D Engineer
- R&D Manager
- IP Professional
- Industry Leading Data Capabilities
- Powerful AI technology
- Patent DNA Extraction
Browse by: Latest US Patents, China's latest patents, Technical Efficacy Thesaurus, Application Domain, Technology Topic, Popular Technical Reports.
© 2024 PatSnap. All rights reserved.Legal|Privacy policy|Modern Slavery Act Transparency Statement|Sitemap|About US| Contact US: help@patsnap.com