Method for separating cellulose from bagasse and performing enzymolysis
A sugarcane bagasse and cellulose technology, used in fiber raw materials, fiber raw material processing, papermaking, etc., can solve the problems of general removal of lignin and hemicellulose, improve the enzymatic sugar production efficiency and enzymatic hydrolysis rate, and improve Enzymatic hydrolysis efficiency and mild reaction conditions
- Summary
- Abstract
- Description
- Claims
- Application Information
AI Technical Summary
Problems solved by technology
Method used
Examples
Embodiment 1
[0067] S1. Add 60% (v / v) ethanol aqueous solution to the bagasse raw material according to the ratio of absolute dry mass volume ratio 1g: 10mL, and then add 0.005mol / L ethanol aqueous solution of CuCl 2 , react in a high-pressure reactor at 160°C. After the reaction time reaches 10 minutes, stop heating, and immediately use condensed water to lower the reaction to room temperature, and use vacuum filtration to separate the pretreatment residue.
[0068] The component analysis of the pretreatment residue shows that the removal rates of hemicellulose and lignin can reach 26.5% and 35.4%, respectively, and the retention rate of cellulose can reach 99.6%.
[0069] S2. Take 2 grams (on an absolute dry basis) of the pretreatment residue, add 20 FPU of cellulase and 100 mL of acetic acid-sodium acetate buffer solution with pH=4.8 for enzymatic hydrolysis. During the enzymolysis process, the temperature was controlled at 50° C., and the rotation speed was 150 rpm. After 72 hours of ...
Embodiment 2
[0072] S1. Add 60% (v / v) ethanol aqueous solution to the bagasse raw material according to the ratio of absolute dry mass volume ratio of 1g: 10mL, and then add 0.01mol / L ethanol aqueous solution of CuCl 2 , react in a high-pressure reactor at 160°C. After the reaction time reaches 10 minutes, stop heating, and immediately use condensed water to lower the reaction to room temperature, and use vacuum filtration to separate the pretreatment residue.
[0073] The component analysis of the pretreatment residue shows that the removal rates of hemicellulose and lignin can reach 50.8% and 45.2%, respectively, and the retention rate of cellulose can reach 98.9%.
[0074] S2. Take 2 grams (on an absolute dry basis) of the pretreatment residue, add 20 FPU of cellulase and 100 mL of acetic acid-sodium acetate buffer solution with pH=4.8 for enzymatic hydrolysis. During the enzymolysis process, the temperature was controlled at 50° C., and the rotation speed was 150 rpm. After 72 hours o...
Embodiment 3
[0077] S1. Add 60% (v / v) ethanol aqueous solution to the bagasse raw material according to the ratio of absolute dry mass volume ratio 1g: 10mL, and then add 0.025mol / L ethanol aqueous solution of CuCl 2 , react in a high-pressure reactor at 160°C. After the reaction time reaches 10 minutes, stop heating, and immediately use condensed water to lower the reaction to room temperature, and use vacuum filtration to separate the pretreatment residue.
[0078] The component analysis of the pretreatment residue shows that the removal rates of hemicellulose and lignin can reach 83.2% and 71.4%, respectively, and the retention rate of cellulose can reach 95.0%.
[0079] S2. Take 2 grams (on an absolute dry basis) of the pretreatment residue, add 20 FPU of cellulase and 100 mL of acetic acid-sodium acetate buffer solution with pH=4.8 for enzymatic hydrolysis. During the enzymolysis process, the temperature was controlled at 50° C., and the rotation speed was 150 rpm. After 72 hours of ...
PUM
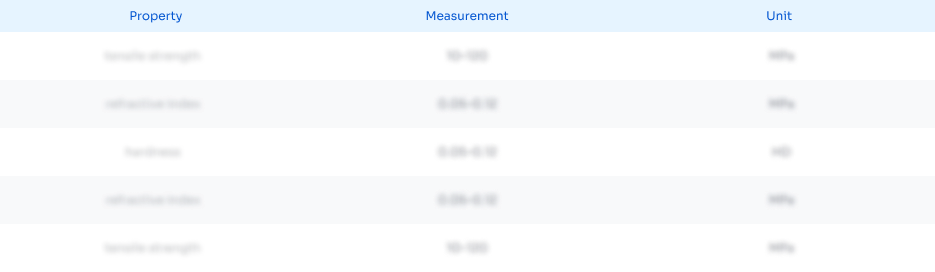
Abstract
Description
Claims
Application Information

- R&D Engineer
- R&D Manager
- IP Professional
- Industry Leading Data Capabilities
- Powerful AI technology
- Patent DNA Extraction
Browse by: Latest US Patents, China's latest patents, Technical Efficacy Thesaurus, Application Domain, Technology Topic, Popular Technical Reports.
© 2024 PatSnap. All rights reserved.Legal|Privacy policy|Modern Slavery Act Transparency Statement|Sitemap|About US| Contact US: help@patsnap.com