Method for purifying aluminum-silicon-iron alloy through high-temperature and low-temperature two-step remelting centrifugal separation
A centrifugal separation and ferroalloy technology, applied in the field of smelting, can solve the problems of inability to carry out high-efficiency and large-scale practical applications, and achieve significant social and economic benefits, rational use of resources, and the effect of reducing iron content
- Summary
- Abstract
- Description
- Claims
- Application Information
AI Technical Summary
Problems solved by technology
Method used
Image
Examples
Embodiment 1
[0030] A high-temperature, low-temperature two-step remelting centrifugal separation method for purifying Al-Si-Fe alloy, the process flow chart is as follows figure 2 shown, including the following steps:
[0031] Put 100kg of Al-Si-Fe alloy into an intermediate frequency furnace for high-temperature smelting, the temperature of the molten material is 1400-1600°C, and the Al-Si-Fe alloy composition is 52.45% of Al, 41.98% of Si, and 2.65% of Fe. Al-Si-Fe alloy melt; cast the melt in a mold, then cool down to 900°C at 2°C / min, keep it at this temperature for 120min, let the alloy phase precipitate and grow, and then cool naturally to room temperature to obtain first-grade aluminum Ferrosilicon alloy block. Such as figure 1 As shown, the alloy phase diagram of the present invention shows that when the cooling temperature drops to 950-1000°C, silicon crystals first precipitate and grow up, and as the cooling temperature decreases, the silicon content in the melt gradually dec...
Embodiment 2
[0034] A high-temperature, low-temperature two-step remelting centrifugal separation method for purifying Al-Si-Fe alloy, the process flow chart is as follows figure 2 shown, including the following steps:
[0035] Put 100kg of Al-Si-Fe alloy into an intermediate frequency furnace for high-temperature smelting, the temperature of the molten material is 1400-1600°C, and the Al-Si-Fe alloy composition is 52.45% by Al, 41.98% by Si and 2.65% by Fe. Aluminum-silicon-iron alloy melt; cast the melt in a mold, then cool down to 950°C at 5°C / min, keep it at this temperature for 90min, let the alloy phase precipitate and grow, and then cool naturally to room temperature to obtain first-grade aluminum Ferrosilicon block. Such as figure 1 As shown, the phase diagram of the alloy of the present invention shows that when the cooling temperature drops to 950-1000°C, silicon crystals first precipitate and grow up. As the cooling temperature decreases, the silicon content in the melt gradu...
Embodiment 3
[0038] A high-temperature, low-temperature two-step remelting centrifugal separation method for purifying Al-Si-Fe alloy, the process flow chart is as follows figure 2 shown, including the following steps:
[0039] Put 100kg of Al-Si-Fe alloy into an intermediate frequency furnace for high-temperature smelting, the temperature of the molten material is 1400-1600°C, and the Al-Si-Fe alloy composition is 52.45% by Al, 41.98% by Si and 2.65% by Fe. Aluminum-silicon-iron alloy melt; cast the melt in a mold, then cool down to 950°C at 5°C / min, keep it at this temperature for 90min, let the alloy phase precipitate and grow, and then cool naturally to room temperature to obtain first-grade aluminum Ferrosilicon block. Such as figure 1 As shown, the phase diagram of the alloy of the present invention shows that when the cooling temperature drops to 950-1000°C, silicon crystals first precipitate and grow up. As the cooling temperature decreases, the silicon content in the melt gradu...
PUM
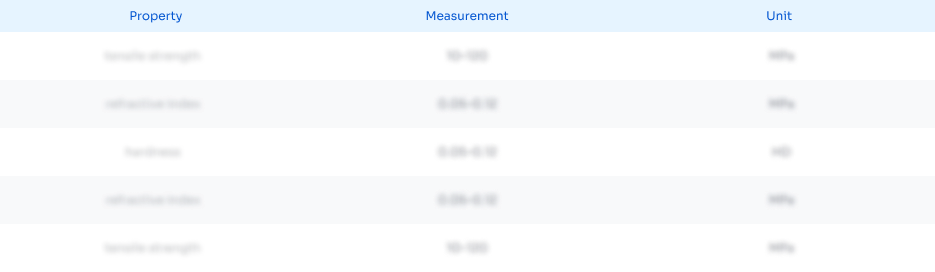
Abstract
Description
Claims
Application Information

- R&D
- Intellectual Property
- Life Sciences
- Materials
- Tech Scout
- Unparalleled Data Quality
- Higher Quality Content
- 60% Fewer Hallucinations
Browse by: Latest US Patents, China's latest patents, Technical Efficacy Thesaurus, Application Domain, Technology Topic, Popular Technical Reports.
© 2025 PatSnap. All rights reserved.Legal|Privacy policy|Modern Slavery Act Transparency Statement|Sitemap|About US| Contact US: help@patsnap.com