Preparation method of two-component functional filler composite coating layer for space high-energy proton radiation protection
A high-energy proton and radiation protection technology, applied in coatings, nuclear power generation, epoxy resin coatings, etc., can solve problems such as limited effects, achieve simple methods, improve the ability to shield gamma rays and neutrons, and simplify the preparation process Effect
- Summary
- Abstract
- Description
- Claims
- Application Information
AI Technical Summary
Problems solved by technology
Method used
Image
Examples
Embodiment 1
[0030] 1. Preparation of composite powder
[0031] Mix gadolinium oxide and tungsten with a mass ratio of 1:1 and pour them into a ball mill jar so that the ball-to-material ratio in the ball mill jar is 2:1, put the ball mill jar into the ball mill, and use a speed of 200rpm under normal pressure , ball milling for 12 hours, after the ball milling, take out the ball material, separate the ball material, and obtain a composite powder with a core-shell structure;
[0032] 2. Composite powder
[0033] Mix the composite powder obtained above with epoxy resin, wherein the mass fraction of the composite powder is 10%, use a three-roll mill to fully grind and mix, and the grinding time is 10 minutes. After the grinding is completed, the mixed powder is sprayed The obtained slurry was coated on the surface of the protected object to form a coating with a thickness of 100 μm, and the coating was placed in a vacuum drying oven and dried at 30° C. for 6 hours to obtain a composite coat...
Embodiment 2
[0036] 1. Preparation of composite powder
[0037] Mix the erbium oxide and tantalum with a mass ratio of 2:1 and pour it into the ball mill jar so that the ball-to-material ratio in the ball mill jar is 2:1, put the ball mill jar into the ball mill, and use a rotating speed of 200rpm under the condition of Ar protection , ball milling for 24 hours, after the ball milling, take out the ball material, separate the ball material, and obtain a composite powder with a core-shell structure;
[0038] 2. Composite powder
[0039] Mix the composite powder obtained above with epoxy resin, wherein the mass fraction of the composite powder is 30%, use a three-roll mill to fully grind and mix, and the grinding time is 10 minutes. The mixed slurry was coated on the surface of the protected object to form a coating with a thickness of 500um, and the coating was placed in a vacuum drying oven and dried at 50°C for 8 hours to obtain a composite coating.
Embodiment 3
[0041] 1. Preparation of composite powder
[0042] Mix cerium oxide and bismuth elemental substances with a mass ratio of 5:1 and pour them into a ball mill jar, so that the ball-to-material ratio in the ball mill jar is 2:1, put the ball mill jar into the ball mill, and use a rotating speed of 400rpm under the protection of Ar , ball milling for 24 hours, after the ball milling, take out the ball material, separate the ball material, and obtain a composite powder with a core-shell structure;
[0043] 2. Composite powder
[0044] Mix the composite powder obtained above with epoxy resin, wherein the mass fraction of the composite powder is 30%, use a three-roll mill to fully grind and mix, and the grinding time is 10 minutes. The mixed slurry was coated on the surface of the protected object to form a coating with a thickness of 500um, and the coating was placed in a vacuum drying oven and dried at 50°C for 8 hours to obtain a composite coating.
PUM
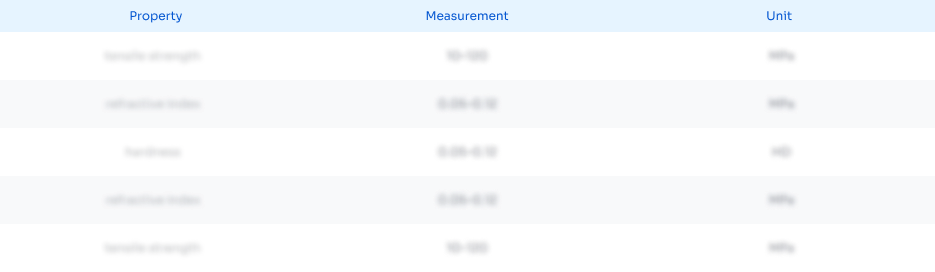
Abstract
Description
Claims
Application Information

- R&D
- Intellectual Property
- Life Sciences
- Materials
- Tech Scout
- Unparalleled Data Quality
- Higher Quality Content
- 60% Fewer Hallucinations
Browse by: Latest US Patents, China's latest patents, Technical Efficacy Thesaurus, Application Domain, Technology Topic, Popular Technical Reports.
© 2025 PatSnap. All rights reserved.Legal|Privacy policy|Modern Slavery Act Transparency Statement|Sitemap|About US| Contact US: help@patsnap.com