Preparation method of dry powder extinguishing agent containing allophanate
A dry powder fire extinguishing agent, allophanate technology, applied in fire protection equipment and other directions, can solve the problems of easy moisture absorption and agglomeration, poor fluidity, unable to meet the needs of fire safety situation, etc., to achieve good storage, good hydrophobicity and The effect of fluidity and outstanding fire extinguishing efficiency
- Summary
- Abstract
- Description
- Claims
- Application Information
AI Technical Summary
Problems solved by technology
Method used
Image
Examples
Embodiment 1
[0030] 30g potassium allophanate, 18g potassium bicarbonate, 24g ammonium phosphomolybdate, 12g zinc borate and 16g urea are placed in a planetary ball mill, crushed and mixed by mechanical force to obtain the fire extinguishing agent precursor, wherein the ball mill speed is 300r / min, the grinding time is 1h, and the mass ratio of grinding body to mixture is 2:1.
[0031] Take 100g of the above-mentioned fire extinguishing agent precursor and add it to 500ml of deionized water, and use a cantilever stirrer to evenly stir to obtain an emulsion. The speed of the cantilever stirrer is 400r / min, and the stirring time is 10min;
[0032] Transfer the emulsion to a polytetrafluoroethylene reactor, and react to obtain the reaction product after the temperature program is raised. The temperature rise program is: raise the temperature from 25°C to 100°C in 30 minutes, keep it for 1 hour, and then raise the temperature from 100°C to 160°C in 60 minutes. , kept for 2h, cooled to room tem...
Embodiment 2
[0038] 45g of potassium allophanate, 15g of potassium bicarbonate, 12g of zinc carbonate, 12g of ammonium molybdate and 16g of molybdenum disulfide were placed in a planetary ball mill, pulverized and mixed by mechanical force to obtain a fire extinguishing agent precursor. The rotational speed of the ball mill is 350r / min, the grinding time is 1h, and the mass ratio of the grinding body to the mixture is 2:1.
[0039] Take 100g of the fire extinguishing agent precursor and add it to 500ml of deionized water, and stir evenly with a cantilever stirrer to obtain an emulsion. The speed of the cantilever stirrer is 450r / min, and the stirring time is 10min;
[0040] Transfer the emulsion to a polytetrafluoroethylene reactor, and react to obtain the reaction product after the temperature program is raised. The temperature rise program is: raise the temperature from 25°C to 100°C in 30 minutes, keep it for 1 hour, and then raise the temperature from 100°C to 160°C in 60 minutes. , ke...
Embodiment 3
[0046] Put 40g of sodium allophanate, 20g of sodium bicarbonate, 14g of manganese hypophosphite, 14g of cetyltrimethylammonium bromide and 12g of aluminum silicate in a planetary ball mill, crush and mix them by mechanical force to obtain a fire extinguishing agent Precursor. The rotational speed of the ball mill is 350r / min, the grinding time is 1h, and the mass ratio of the grinding body to the mixture is 2:1.
[0047] Take 100g of the fire extinguishing agent precursor and add it to 500ml of deionized water, and use a cantilever stirrer to evenly stir to obtain an emulsion. The speed of the cantilever stirrer is 500r / min, and the stirring time is 10min;
[0048] Transfer the emulsion to a polytetrafluoroethylene reactor, and react to obtain the reaction product after heating up the temperature. The heating program is as follows: raise the temperature from 25°C to 100°C in 30 minutes, keep it for 2 hours, and then raise the temperature from 100°C to 160°C in 60 minutes , ke...
PUM
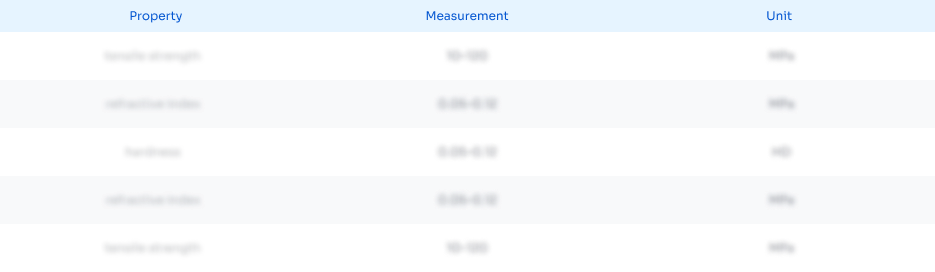
Abstract
Description
Claims
Application Information

- R&D
- Intellectual Property
- Life Sciences
- Materials
- Tech Scout
- Unparalleled Data Quality
- Higher Quality Content
- 60% Fewer Hallucinations
Browse by: Latest US Patents, China's latest patents, Technical Efficacy Thesaurus, Application Domain, Technology Topic, Popular Technical Reports.
© 2025 PatSnap. All rights reserved.Legal|Privacy policy|Modern Slavery Act Transparency Statement|Sitemap|About US| Contact US: help@patsnap.com