Composite catalyst and method for preparing trimellitic anhydride
A technology of composite catalyst and trimellitic anhydride, which is applied in the direction of chemical instruments and methods, organic compound/hydride/coordination complex catalyst, physical/chemical process catalyst, etc., can solve the problems affecting the appearance and color number of the final product, and the conversion of trimethylbenzene Low production rate, many impurities in the finished product, etc., to achieve the effect of appearance and color number guarantee, reduction of production cost and high yield
- Summary
- Abstract
- Description
- Claims
- Application Information
AI Technical Summary
Problems solved by technology
Method used
Image
Examples
Embodiment 1
[0031] First, add 200kg of mesitylene, 600kg of acetic acid, and 14kg of composite catalyst in the mixing kettle, wherein in the composite catalyst, there are 2.2kg of cobalt acetate, 6.6kg of manganese acetate, 4.2kg of tetrabromoethane, and 1kg of zirconium acetate, start stirring and mixing, and heat up To 80 ℃, so that trimethylbenzene and solvent miscibility;
[0032] Then the mixed material is transferred to the oxidation kettle, and the air is introduced to pressurize. The temperature of the reaction is controlled at 210°C, the pressure is controlled at 1.8Mpa, and the reaction time is 70 minutes. When the oxygen content of the tail gas reaches 15-20%, the oxidation reaction ends;
[0033] Then control the temperature of the anhydride-forming kettle at 180°C, dehydrate the oxidized material into crude anhydride in the anhydride-forming kettle, send the dilute acetic acid produced during the anhydride-forming process into the rectifying kettle, and reuse it after concentr...
Embodiment 2
[0036] First add 200kg of trimethylene, 600kg of acetic acid, and 12kg of composite catalyst in the mixing kettle, wherein in the composite catalyst, 1.5kg of cobalt acetate, 3kg of manganese acetate, 3kg of tetrabromoethane, 4.5kg of zirconium acetate, start stirring and mixing, and heat up to 80°C, make trimethylbenzene and solvent miscible;
[0037] Then transfer the mixed material to the oxidation kettle, feed air to pressurize, control the temperature of the reaction at 180°C, the pressure at 1.0Mpa, the reaction time is 90 minutes, and the oxidation reaction ends when the oxygen content of the tail gas reaches 15-20%.
[0038]Then control the temperature of the anhydride-forming kettle at 180°C, dehydrate the oxidized material into crude anhydride in the anhydride-forming kettle, send the dilute acetic acid produced during the anhydride-forming process into the rectifying kettle, and reuse it after concentration;
[0039] Rectification step: control the temperature of th...
Embodiment 3
[0041] First, add 200kg of mesitylene, 750kg of acetic acid, and 8kg of composite catalyst in the mixing kettle, of which, in the composite catalyst, 1.3kg of cobalt acetate, 2.5kg of manganese acetate, 1kg of tetrabromoethane, and 3.2kg of zirconium acetate are started to stir and mix, and the temperature is raised To 80 ℃, so that trimethylbenzene and solvent miscibility;
[0042] Then transfer the mixed material to the oxidation kettle, feed air to pressurize, control the temperature of the reaction at 200°C, the pressure at 1.5Mpa, and the reaction time is 80 minutes. When the oxygen content in the tail gas reaches 15-20%, the oxidation reaction ends;
[0043] Then control the temperature of the anhydride-forming kettle at 180°C, dehydrate the oxidized material into crude anhydride in the anhydride-forming kettle, send the dilute acetic acid produced during the anhydride-forming process into the rectifying kettle, and reuse it after concentration;
[0044] Rectification st...
PUM
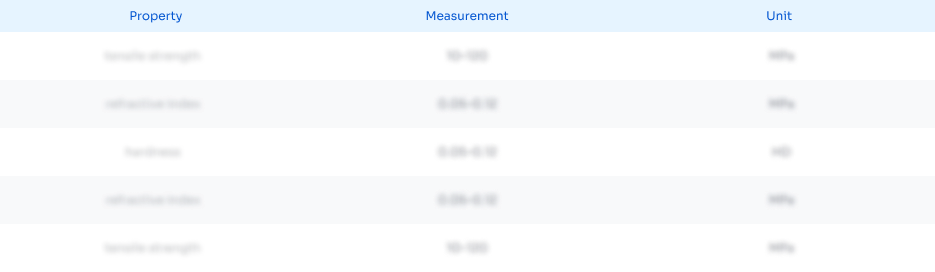
Abstract
Description
Claims
Application Information

- R&D
- Intellectual Property
- Life Sciences
- Materials
- Tech Scout
- Unparalleled Data Quality
- Higher Quality Content
- 60% Fewer Hallucinations
Browse by: Latest US Patents, China's latest patents, Technical Efficacy Thesaurus, Application Domain, Technology Topic, Popular Technical Reports.
© 2025 PatSnap. All rights reserved.Legal|Privacy policy|Modern Slavery Act Transparency Statement|Sitemap|About US| Contact US: help@patsnap.com