Preparation method and application of cerium dioxide nanowire
A ceria and nanowire technology, applied in the preparation/processing of rare earth metal compounds, chemical instruments and methods, ceria/ceria hydroxide, etc., can solve the problem of uneven distribution of ceria nanowires and small aspect ratio and other problems, to achieve the effect of low cost, good stability and cost reduction
- Summary
- Abstract
- Description
- Claims
- Application Information
AI Technical Summary
Problems solved by technology
Method used
Image
Examples
Embodiment 1
[0029] A preparation method of ceria nanowires, comprising the following steps:
[0030] 1) Dissolve 1.74g cerium nitrate hexahydrate and 0.1269g ammonium molybdate tetrahydrate in 40mL distilled water to obtain a mixed solution of cerium nitrate and ammonium molybdate; dissolve 19.2g sodium hydroxide in 40mL distilled water to obtain sodium hydroxide solution;
[0031] 2) Add the sodium hydroxide solution dropwise into the mixed solution of cerium nitrate and ammonium molybdate under constant stirring, and keep stirring for 30 minutes to obtain a new mixed solution;
[0032] 3) The new mixed solution was transferred to a 100 mL polytetrafluoroethylene-lined stainless steel autoclave, and reacted at 120° C. for 36 h. After the reaction was finished and cooled naturally, the lower layer of precipitate was left.
[0033] 4) Centrifugal washing with deionized water and ethanol solution for several times to neutrality, and drying at 60° C. for 8 hours to obtain a molybdenum-ceri...
Embodiment 2
[0036] A preparation method of ceria nanowires, comprising the following steps:
[0037] 1) Dissolve 1.74g of cerium nitrate hexahydrate and 0.06345g of ammonium molybdate tetrahydrate in 40mL of distilled water to obtain a mixed solution of cerium nitrate and ammonium molybdate; dissolve 19.2g of sodium hydroxide in 40mL of distilled water to obtain sodium hydroxide solution;
[0038] 2) Add the sodium hydroxide solution dropwise into the mixed solution of cerium nitrate and ammonium molybdate under constant stirring, and keep stirring for 30 minutes to obtain a new mixed solution;
[0039] 3) The new mixed solution was transferred to a 100 mL polytetrafluoroethylene-lined stainless steel autoclave, and reacted at 80° C. for 48 h. After the reaction was finished and cooled naturally, the lower layer of precipitate was left.
[0040] 4) Centrifugal washing with deionized water and ethanol solution for several times to neutrality, and drying at 50° C. for 8 hours to obtain a ...
Embodiment 3
[0043] A preparation method of ceria nanowires, comprising the following steps:
[0044] 1) Dissolve 1.74g cerium nitrate hexahydrate and 0.0187g sodium molybdate dihydrate in 40mL distilled water to obtain a mixed solution of cerium nitrate and ammonium molybdate; dissolve 19.2g sodium hydroxide in 40mL distilled water to obtain sodium hydroxide solution;
[0045] 2) Add the sodium hydroxide solution dropwise into the mixed solution of cerium nitrate and sodium molybdate under continuous stirring, and keep stirring for 30 minutes to obtain a new mixed solution;
[0046] 3) The new mixed solution was transferred to a 100 mL polytetrafluoroethylene-lined stainless steel autoclave, and reacted at 100° C. for 24 h. After the reaction was finished and cooled naturally, the lower layer of precipitate was left.
[0047] 4) Centrifugal washing with deionized water and ethanol solution several times to neutrality, and drying at 80° C. for 6 hours to obtain a molybdenum-cerium precur...
PUM
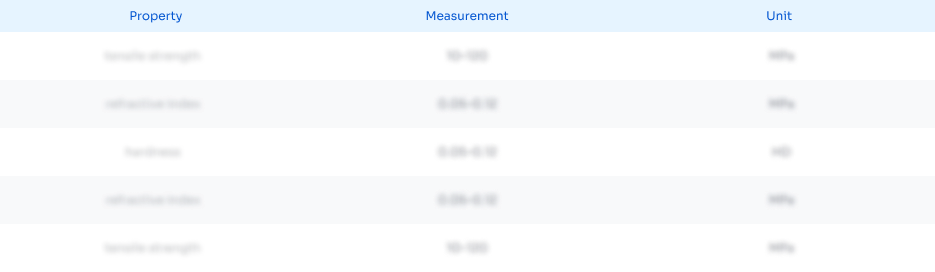
Abstract
Description
Claims
Application Information

- Generate Ideas
- Intellectual Property
- Life Sciences
- Materials
- Tech Scout
- Unparalleled Data Quality
- Higher Quality Content
- 60% Fewer Hallucinations
Browse by: Latest US Patents, China's latest patents, Technical Efficacy Thesaurus, Application Domain, Technology Topic, Popular Technical Reports.
© 2025 PatSnap. All rights reserved.Legal|Privacy policy|Modern Slavery Act Transparency Statement|Sitemap|About US| Contact US: help@patsnap.com