Aluminum alloy internal corner template and processing method thereof
A technology of internal corner templates and processing methods, which is applied to the preparation of formwork/formwork/work frame, formwork/formwork components, and building components on site, which can solve the problems of large environmental pollution, low process efficiency, and high energy consumption. problem, to achieve the effect of high structural rigidity, low production cost and improved strength
- Summary
- Abstract
- Description
- Claims
- Application Information
AI Technical Summary
Problems solved by technology
Method used
Image
Examples
Embodiment 1
[0035] refer to figure 1 , this embodiment provides an aluminum alloy female corner end plate, including a connecting end face 100, wherein the connecting end face 100 is installed at the end of the female corner formwork profile, which includes an end panel 101, and the shape of the end panel 101 is a flat plate, wherein the end The panel 101 can be placed in the cavity of the profile for easy connection.
[0036] Further, the end panel 101 is provided with a connecting boss 102 along the outer periphery. Preferably, the range of the connecting boss 102 is consistent with the cross-section of the profile to be connected, and the end panel 101 and the connecting boss 102 are integrally formed. 101 can increase the connection area when it is connected with the profile. The connection end face 100 is integrally formed by pressure casting, which has the advantages of high productivity and high dimensional accuracy of the product.
Embodiment 2
[0038] refer to Figure 1~3 , is the second embodiment of the present invention, this embodiment is based on the previous embodiment, and the difference from the previous embodiment is that this embodiment provides a female corner formwork, which includes a connecting end face 100 and a connecting profile 200, wherein The connecting profile 200 is an aluminum alloy profile commonly used in the internal corner formwork, and its cross section is similar to C-shaped, consisting of four planes, that is, there is an opening, which is biased towards operation and installation; wherein, the connecting boss 102 is embedded in the connecting profile 200, The outer surface of the connection boss 102 is in contact with the inner surface of the connection profile 200 . Therefore, the connecting boss 102 is integrally installed in the connecting profile 200 to increase the connecting area, and the end panel 101 and the end of the connecting profile 200 are located on the same plane, which ...
Embodiment 3
[0042] refer to Figure 4~6, is the third embodiment of the present invention, this embodiment is based on the first embodiment, and the difference from the previous embodiment is that this embodiment provides an easy-to-detach internal corner formwork, specifically: including the connection end surface 100 . The connection profile 200, wherein the connection profile 200 is an aluminum alloy profile commonly used in the internal corner formwork, and its cross section is similar to a C-type, consisting of four planes, that is, there is an opening, which is biased towards operation and installation; wherein, the connection boss 102 Embedded in the connection profile 200 , the outer surface of the connection boss 102 is in contact with the inner surface of the connection profile 200 . Therefore, the connecting boss 102 is integrally installed in the connecting profile 200 to increase the connecting area, and the end panel 101 and the end of the connecting profile 200 are located ...
PUM
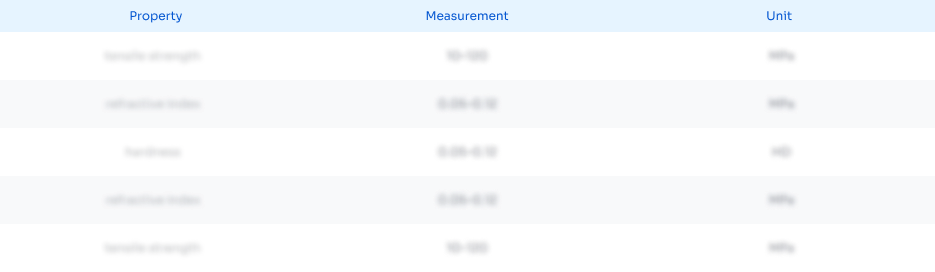
Abstract
Description
Claims
Application Information

- R&D Engineer
- R&D Manager
- IP Professional
- Industry Leading Data Capabilities
- Powerful AI technology
- Patent DNA Extraction
Browse by: Latest US Patents, China's latest patents, Technical Efficacy Thesaurus, Application Domain, Technology Topic, Popular Technical Reports.
© 2024 PatSnap. All rights reserved.Legal|Privacy policy|Modern Slavery Act Transparency Statement|Sitemap|About US| Contact US: help@patsnap.com