Tripolyphosphate/carbon nitride nano composite material, preparation method thereof and application of the same in water-based anticorrosive paint
A technology of nano-composite materials and tripolyphosphate, which is applied in the field of coatings, can solve the problems of poor compatibility, affecting the protective performance of coatings, and easy agglomeration, etc., and achieve the effect of enhancing performance, improving physical barrier performance, and simple process
- Summary
- Abstract
- Description
- Claims
- Application Information
AI Technical Summary
Problems solved by technology
Method used
Image
Examples
preparation example Construction
[0034] A preparation method of tripolyphosphate / carbon nitride nanocomposite material, comprising the steps of:
[0035] Step 1, use melamine as raw material to prepare bulk graphite phase carbon nitride (g-C 3 N 4 ), and obtained g-C by stripping 3 N 4Nanosheets.
[0036] Step 2, g-C 3 N 4 Functionalization of nanosheets: take g-C in step 1 3 N 4 The nanosheets were ultrasonically dispersed in an ethanol solution with a mass fraction of 75%-90% at room temperature, then transferred to a water bath at 50-90 °C, and then the silane coupling agent was added dropwise, and kept stirring for 6-12 h; the reaction was completed Afterwards, cooling, centrifugation, washing with absolute ethanol and deionized water, and drying in sequence to obtain functionalized g-C 3 N 4 Nanosheets.
[0037] Step 3, g-C 3 N 4 Carboxylation of nanosheets: take the functionalized g-C in step 2 3 N 4 Ultrasonic dispersion of nanosheets in toluene, then drop an appropriate amount of succini...
Embodiment 1
[0054] (1) Weigh 20 g of melamine into a closed container, place it in a tube furnace, raise the temperature to 500 °C at a rate of 10 °C / min, keep it warm for 5 hours, and cool it down to room temperature naturally to obtain the bulk g-C 3 N 4 ; Then, the above bulk phase g-C 3 N 4 Spread it on the bottom of an alumina crucible, raise the temperature to 550 °C at a rate of 15 °C / min in a nitrogen atmosphere, keep it warm for 2 hours, and then cool it down to room temperature naturally to obtain thermal peeling g-C 3 N 4 Nanosheets.
[0055] (2) g-C 3 N 4 Nanosheet functionalization: take 1.0 g of g-C in step (1) 3 N 4 The nanosheets were ultrasonically dispersed in 85% ethanol solution at room temperature, and then transferred to a water bath at 70 °C; 20 g of KH-550 was added to the above suspension at a speed of 400 r / min, and the reaction was incubated and stirred for 10 h; After the reaction was completed, cooling, centrifugation, washing with absolute ethanol and...
Embodiment 2
[0060] (1) Weigh 20 g of melamine into a closed container, place it in a tube furnace, raise the temperature to 500 °C at a rate of 10 °C / min, keep it warm for 5 hours, and cool it down to room temperature naturally to obtain the bulk g-C 3 N 4 ; Then, the above bulk phase g-C 3 N 4 Spread it on the bottom of an alumina crucible, raise the temperature to 550 °C at a rate of 15 °C / min in a nitrogen atmosphere, keep it warm for 2 hours, and then cool it down to room temperature naturally to obtain thermal peeling g-C 3 N 4 Nanosheets.
[0061] (2) g-C 3 N 4 Nanosheet functionalization: Take 2.0 g of g-C from step (1) 3 N 4 The nanosheets were ultrasonically dispersed in 85% ethanol solution at room temperature, and then transferred to a water bath at 70 °C; 50 g of KH-560 was added to the above suspension at a speed of 400 r / min, and the reaction was incubated and stirred for 10 h; After the reaction was completed, cooling, centrifugation, washing with absolute ethanol a...
PUM
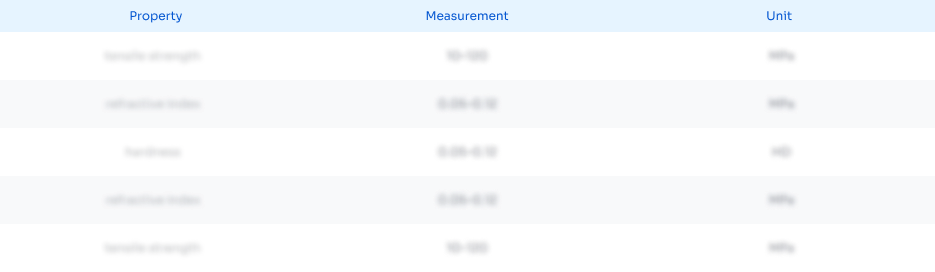
Abstract
Description
Claims
Application Information

- R&D
- Intellectual Property
- Life Sciences
- Materials
- Tech Scout
- Unparalleled Data Quality
- Higher Quality Content
- 60% Fewer Hallucinations
Browse by: Latest US Patents, China's latest patents, Technical Efficacy Thesaurus, Application Domain, Technology Topic, Popular Technical Reports.
© 2025 PatSnap. All rights reserved.Legal|Privacy policy|Modern Slavery Act Transparency Statement|Sitemap|About US| Contact US: help@patsnap.com