Anti-glare film and preparation method thereof
An anti-glare and anti-glare layer technology, applied in the field of composite films, can solve the problems of limited surface hardness improvement, poor particle adhesion, poor temperature resistance, etc., and achieve high particle adhesion, high surface hardness, flexibility and processing effects
- Summary
- Abstract
- Description
- Claims
- Application Information
AI Technical Summary
Problems solved by technology
Method used
Image
Examples
Embodiment 1
[0044] First, heat-curable silicone resin, nano-silica, aminopropyltriethoxysilane (KH-550), and aromatic hydrocarbon solvents are mixed to form a coating composition, and then the coating composition is sprayed on a high-temperature-resistant plastic substrate above to obtain a dry thickness of 3 μm; again dry the prepared coated high-temperature resistant plastic substrate at 50-100°C for 20 minutes; finally heat and cure the prepared dried coated high-temperature-resistant plastic substrate at 150-200°C The anti-glare film was obtained in 30 minutes.
Embodiment 2
[0046] First, heat-curable silicone resin, nano silicon dioxide, glycidyl ether oxypropyl trimethoxysilane (KH-560), and aliphatic hydrocarbon solvent are mixed into a coating composition, and then the coating composition is sprayed on on the high-temperature-resistant plastic substrate to obtain a dry thickness of 5 μm; again, dry the prepared high-temperature-resistant plastic substrate at 50-100°C for 22 minutes; finally, dry the prepared high-temperature-resistant coating at 150-200°C The plastic substrate was heated and cured for 34 minutes to obtain an anti-glare film.
Embodiment 3
[0048] First, heat-curable silicone resin, nano-silica, methacryloxypropyltrimethoxysilane (KH-570), and alcohol solvents are mixed to form a coating composition, and then the coating composition is sprayed on on the high-temperature-resistant plastic substrate to obtain a dry thickness of 7 μm; again, dry the prepared coating on the high-temperature-resistant plastic substrate at 50-100°C for 25 minutes; finally, dry the prepared high-temperature-resistant coating at 150-200°C The plastic substrate was heated and cured for 38 minutes to obtain an anti-glare film.
PUM
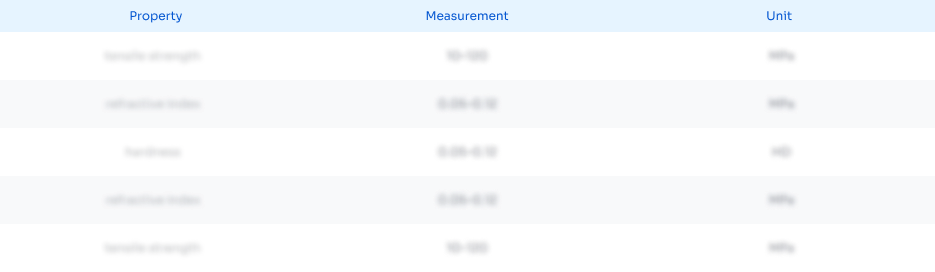
Abstract
Description
Claims
Application Information

- Generate Ideas
- Intellectual Property
- Life Sciences
- Materials
- Tech Scout
- Unparalleled Data Quality
- Higher Quality Content
- 60% Fewer Hallucinations
Browse by: Latest US Patents, China's latest patents, Technical Efficacy Thesaurus, Application Domain, Technology Topic, Popular Technical Reports.
© 2025 PatSnap. All rights reserved.Legal|Privacy policy|Modern Slavery Act Transparency Statement|Sitemap|About US| Contact US: help@patsnap.com