Preparation method of fiber membrane material for heavy metal ion adsorption
A technology for absorbing heavy metal ions and fibers, which is applied in the fields of alkali metal compounds, chemical instruments and methods, adsorption water/sewage treatment, etc., to achieve enhanced adsorption effect and easy operation
- Summary
- Abstract
- Description
- Claims
- Application Information
AI Technical Summary
Problems solved by technology
Method used
Examples
Embodiment 1
[0024] The agricultural straw waste rice straw is cut and crushed, and the straw fiber with a particle size of 40 mesh is taken, and then impregnated with 30% hydrogen peroxide, and at the same time combined with ozone aeration and ultrasonic induction to convert hydrogen peroxide into hydroxyl radicals, so that the fibers are regenerated. The connection obtained a white rice straw fiber sponge composed of multi-layered thin fiber network, which was then dried at 50 °C to constant weight. Dissolve glucomannan powder in water, stir until dissolved to obtain a homogeneous glucomannan solution, then add sodium hydroxide to the solution to adjust the pH value to 10, and continue stirring for 0.5h to obtain deacetylated glucomannan sugar solution. Immerse the white fiber sponge obtained above in deionized water until the white fiber sponge is completely wetted, then add extracellular polymer, and sodium carbonate to it and stir vigorously for about 1 hour, then add deacetylated glu...
Embodiment 2
[0027] The agricultural straw waste corn stalks are cut and crushed, and the straw fibers with a particle size of 50 mesh are taken, and then impregnated with 20% concentration of hydrogen peroxide. The connection obtained a white cornstalk fiber sponge composed of multilayer thin fiber network, which was then dried at 60 °C to constant weight. Dissolve glucomannan powder in water, stir until dissolved to obtain a homogeneous glucomannan solution, then add potassium hydroxide to the solution to adjust the pH value to 11, and continue stirring for 0.5h to obtain deacetylated glucomannan sugar solution. Immerse the white fiber sponge obtained above in deionized water until the white fiber sponge is completely wetted, then add extracellular polymer and sodium carbonate to it and stir vigorously for about 2 hours, then add deacetylglucomanne to the mixed solution The polysaccharide was stirred continuously and vigorously at 80 °C for 3 h to obtain a white mixture. Add alginic ac...
Embodiment 3
[0030] The bagasse, the agricultural straw waste, is cut and crushed, and the straw fibers with a particle size of 80 mesh are taken, and then impregnated with 25% concentration of hydrogen peroxide. The connection yielded a white bagasse fiber sponge consisting of multilayered thin fiber networks, which was then dried at 70 °C to constant weight. Dissolve glucomannan powder in water, stir until dissolved to obtain a homogeneous glucomannan solution, then add sodium hydroxide to the solution to adjust the pH value to 12, and continue stirring for 0.5h to obtain deacetylated glucomannan sugar solution. Immerse the white fiber sponge obtained above in deionized water until the white fiber sponge is completely wetted, then add extracellular polymer and sodium carbonate to it and stir vigorously for about 3 hours, then add deacetylglucomanne to the mixed solution The polysaccharide was stirred continuously and vigorously at 70 °C for 5 h to obtain a white mixture. Add alginic ac...
PUM
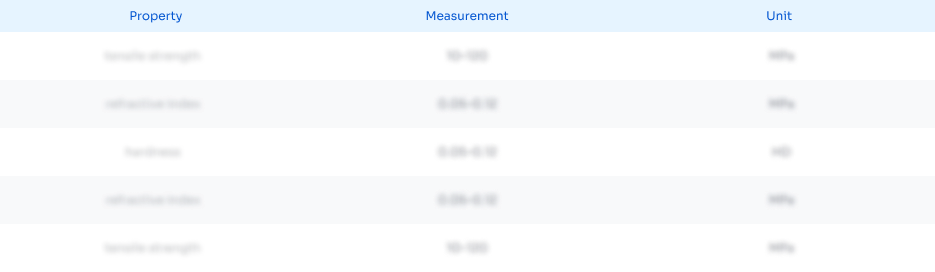
Abstract
Description
Claims
Application Information

- R&D
- Intellectual Property
- Life Sciences
- Materials
- Tech Scout
- Unparalleled Data Quality
- Higher Quality Content
- 60% Fewer Hallucinations
Browse by: Latest US Patents, China's latest patents, Technical Efficacy Thesaurus, Application Domain, Technology Topic, Popular Technical Reports.
© 2025 PatSnap. All rights reserved.Legal|Privacy policy|Modern Slavery Act Transparency Statement|Sitemap|About US| Contact US: help@patsnap.com