Press fitting device with self-locking pressing function and using method
A pressing device and self-locking technology, applied in the field of pressing tooling, can solve the problems of dimensional deviation, insufficient holding pressure, and high labor intensity, so as to achieve the effect of pressing fit and ensuring stability
- Summary
- Abstract
- Description
- Claims
- Application Information
AI Technical Summary
Problems solved by technology
Method used
Image
Examples
Embodiment 1
[0035] Such as Figure 1-2 As shown, there is a press-fitting device with self-locking and pressing, which includes a tooling base plate 25, and guide columns 7 arranged in parallel are fixed on both sides of the top of the tooling base plate 25, and a top plate 11 is fixedly installed on the top of the guide column 7; The lower part of the guide column 7 is slidably fitted with a lifting plate 19 through the guide sliding sleeve 20; the middle part of the bottom end of the lifting plate 19 is fixedly equipped with an upper mold assembly; The lower mold assembly is matched with the lower mold assembly, and the thermoplastic pipe fittings to be processed are press-fitted and formed; the lifting plate 19 is connected with the power device for providing press-fit power through a self-locking linkage mechanism; the power device is fixedly installed on the top plate 11 on. This self-locking compression device can be used for the end shrinkage of thermoplastic pipe fittings. It can...
Embodiment 2
[0045] The operation method of the pressing device with self-locking and pressing comprises the following steps:
[0046] Step 1, heating the end portion of the thermoplastic pipe fitting that needs shrinkage cavity through a heating device;
[0047] Step 2, placing the heated thermoplastic pipe fitting end on the lower half mold 22 of the lower mold assembly;
[0048] Step 3: start the power device, drive the piston rod 12 to go down through the cylinder body 1 of the power device, and drive the third connecting rod 15 to go down through the piston rod 12, and drive the first connecting rod 9 and the second connecting rod through the third connecting rod 15 6. At this time, the first connecting rod 9 and the second connecting rod 6 will straighten, and at the same time, the first connecting rod 9 drives the lifting plate 19 to go down along the guide column 7, and the lifting plate 19 drives the upper mold assembly to press down, and then Compress the end of the thermoplasti...
PUM
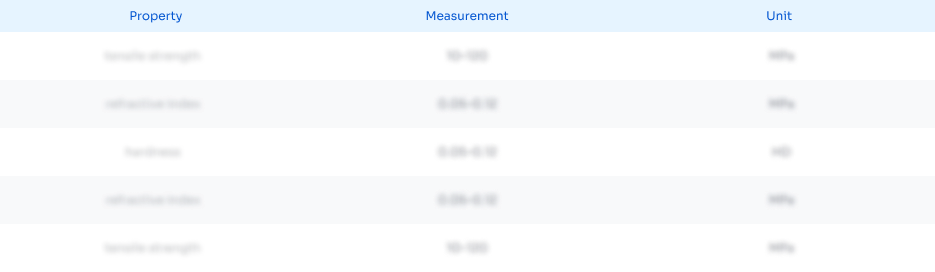
Abstract
Description
Claims
Application Information

- R&D
- Intellectual Property
- Life Sciences
- Materials
- Tech Scout
- Unparalleled Data Quality
- Higher Quality Content
- 60% Fewer Hallucinations
Browse by: Latest US Patents, China's latest patents, Technical Efficacy Thesaurus, Application Domain, Technology Topic, Popular Technical Reports.
© 2025 PatSnap. All rights reserved.Legal|Privacy policy|Modern Slavery Act Transparency Statement|Sitemap|About US| Contact US: help@patsnap.com