Preparation method for reducing apparent density of copper-tin alloy powder
A technology of copper-tin alloy and bulk density, which is applied in the field of preparation of copper-tin alloy powder, can solve the problems of poor compactness and compression performance of applied products, and high bulk density, so as to reduce bulk density, improve sharpness and durability Abrasiveness and the effect of reducing oxidation time
- Summary
- Abstract
- Description
- Claims
- Application Information
AI Technical Summary
Problems solved by technology
Method used
Image
Examples
Embodiment 1
[0023] A kind of preparation method that the present invention discloses reduces the bulk density of copper-tin alloy powder, comprises the following steps:
[0024] (1) choose high-purity copper plate and pure tin powder as raw material, copper content is 84%~86% by mass in the raw material; Tin content is 14%~16% by mass; Copper content is 99.9% in the described high-purity copper plate %~99.95%;
[0025] (2) Water at 0-5°C is used as the source of atomized water during atomization; 1.2kg of charcoal is added during the smelting process, and the steel pouring temperature is 1200°C, and the powder is dehydrated and dried after atomization; the temperature of dehydration and drying treatment is 20 ℃;
[0026] (3) Use the push boat type reduction furnace to feed hydrogen into the reduction; the reduction temperature is 430°C, the boat load is 10kg, the reduction time is 2.3h, the push speed is 620s / boat; the hydrogen flow rate is 4.8m 3 / h;
[0027] (4) Sieve the alloy powde...
Embodiment 2
[0030] A kind of preparation method that the present invention discloses reduces the bulk density of copper-tin alloy powder, comprises the following steps:
[0031] (1) choose high-purity copper plate and pure tin powder as raw material, copper content is 84%~86% by mass in the raw material; Tin content is 14%~16% by mass; Copper content is 99.9% in the described high-purity copper plate %~99.95%;
[0032] (2) Water at 0-5°C is used as the source of atomized water during atomization; 1.0kg of charcoal is added during the smelting process, the temperature of pouring steel is 1250°C, and the powder is dehydrated and dried after atomization; the temperature of dehydration and drying treatment is 16 ℃
[0033] (3) Use a push boat type reduction furnace to feed hydrogen into the reduction; the reduction temperature is 450°C, the boat load is 9kg, the reduction time is 2.0h, the push speed is 600s / boat; the hydrogen flow rate is 4.5m 3 / h;
[0034] (4) sieve the alloy powder obt...
Embodiment 3
[0037] A kind of preparation method that the present invention discloses reduces the bulk density of copper-tin alloy powder, comprises the following steps:
[0038] (1) choose high-purity copper plate and pure tin powder as raw material, copper content is 84%~86% by mass in the raw material; Tin content is 14%~16% by mass; Copper content is 99.9% in the described high-purity copper plate %~99.95%;
[0039] (2) Water at 0-5°C is used as the source of atomized water during atomization; 1.5kg of charcoal is added during the smelting process, the steel pouring temperature is 1300°C, and the powder is dehydrated and dried after atomization; the temperature of dehydration and drying treatment is 20 ℃;
[0040] (3) Use a push boat type reduction furnace to feed hydrogen into the reduction; the reduction temperature is 450°C, the boat load is 11kg, the reduction time is 2.5h, the push speed is 650s / boat; the hydrogen flow rate is 5.0m 3 / h;
[0041] (4) sieve the alloy powder obta...
PUM
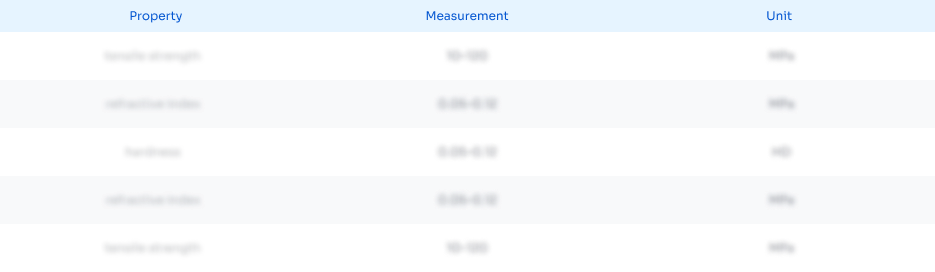
Abstract
Description
Claims
Application Information

- R&D Engineer
- R&D Manager
- IP Professional
- Industry Leading Data Capabilities
- Powerful AI technology
- Patent DNA Extraction
Browse by: Latest US Patents, China's latest patents, Technical Efficacy Thesaurus, Application Domain, Technology Topic, Popular Technical Reports.
© 2024 PatSnap. All rights reserved.Legal|Privacy policy|Modern Slavery Act Transparency Statement|Sitemap|About US| Contact US: help@patsnap.com