Preparation method of carbon material loaded tubular carbon nitride photocatalyst
A technology of carbon materials and catalysts, which is applied in the field of preparation of tubular carbon nitride photocatalysts, can solve the problems of high photogenerated electron-hole recombination rate and narrow visible light absorption range, and achieve fast separation and migration rates and red visible light absorption range. The effect of shifting and low production cost
- Summary
- Abstract
- Description
- Claims
- Application Information
AI Technical Summary
Problems solved by technology
Method used
Image
Examples
Embodiment 1
[0060] A method for preparing a carbon material-supported tubular carbon nitride photocatalyst.
[0061] Peel the pomelo until the pulp is separated, and then process it with a knife, leaving only the white part between the pomelo skin and the pomelo pulp. The white part was cut into small pieces, and dried in a hot blast drying oven at 60°C for 24 hours. Subsequently, after soaking the dried sample in 1 M KOH solution for 12 hours, the obtained sample was freeze-dried for 48 hours. Next, the processed samples were ground in turn to make powder into a crucible and placed in a tube furnace. Nitrogen gas is passed into the tube furnace to carbonize the sample at high temperature in the nitrogen environment. Firstly, it was raised to 300°C for 2.5 hours and kept for 1 hour; then it was raised to 600°C for 1 hour and kept for 0.5 hours; finally it was raised to 800°C for 1 hour and kept for 1 hour, and then cooled to room temperature naturally. Grind the obtained black solid in...
Embodiment 2
[0065] A preparation method of a carbon material-supported tubular carbon nitride photocatalyst is basically the same as the preparation method of the carbon material-supported tubular carbon nitride photocatalyst in Example 1, the only difference being that the quality of the carbon material in Example 2 is 1.4mg.
[0066] The carbon material supported tubular carbon nitride photocatalyst prepared in Example 2 is coded as 2%CCN.
Embodiment 3
[0068] A preparation method of a carbon material-supported tubular carbon nitride photocatalyst is basically the same as the preparation method of the carbon material-supported tubular carbon nitride photocatalyst in Example 1, the only difference being that the quality of the carbon material in Example 2 is 3.5mg.
[0069] The carbon material supported tubular carbon nitride photocatalyst prepared in Example 3 is numbered 5%CCN.
PUM
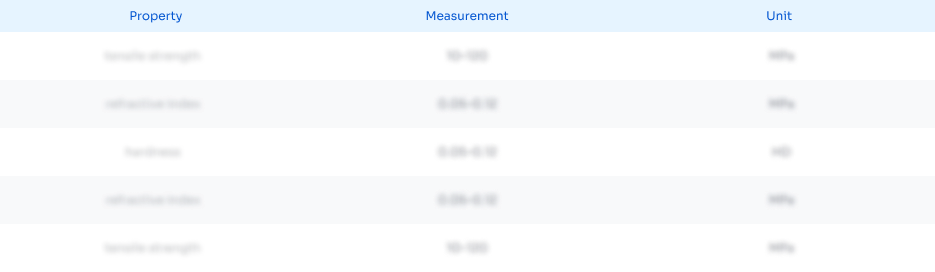
Abstract
Description
Claims
Application Information

- Generate Ideas
- Intellectual Property
- Life Sciences
- Materials
- Tech Scout
- Unparalleled Data Quality
- Higher Quality Content
- 60% Fewer Hallucinations
Browse by: Latest US Patents, China's latest patents, Technical Efficacy Thesaurus, Application Domain, Technology Topic, Popular Technical Reports.
© 2025 PatSnap. All rights reserved.Legal|Privacy policy|Modern Slavery Act Transparency Statement|Sitemap|About US| Contact US: help@patsnap.com