Lead screw mounting structure for grinding machine
A technology of installation structure and screw, which is applied to the parts of grinding machine tools, devices for fixing grinding wheels, grinding/polishing equipment, etc. Reduce problems such as reducing the impact on accuracy and life, improve rigidity and stability, and reduce the amount of overhang
- Summary
- Abstract
- Description
- Claims
- Application Information
AI Technical Summary
Problems solved by technology
Method used
Image
Examples
Embodiment
[0047] refer to figure 1 As shown, this embodiment discloses a screw mounting structure for a grinder, including a screw 1, a support assembly for supporting the rotation of the screw 1, a drive motor for driving the rotation of the screw 1, and a Screw nut 2; the support assembly includes a first support seat 3 and a second support seat 4, the first support seat 3 is provided with a first roller bearing 5, and the second support seat 4 is provided with a flange type sliding sleeve 7 , There is a second roller bearing 6 inside the flange type sliding sleeve 7 .
[0048] Wherein, one end of the screw rod 1 is installed in the first support seat 3 through the first roller bearing 5, and the other end is installed in the second support seat 4 through the second roller bearing 6; the screw rod 1 is located in the first support seat 3 One end of the shaft coupling 8 is installed, and the screw mandrel 1 is connected with the driving motor (not shown in the figure) through the shaf...
Embodiment 2
[0064] This embodiment discloses a numerically controlled vertical grinding machine, which includes a workbench system and an abrasive belt grinding head. The workbench system includes a workbench and an X-axis screw rod. The workbench is installed on the X-axis rail at the top of the frame base through a slider. , the worktable is connected to the X-axis nut seat on the X-axis screw rod, and the X-axis deceleration motor is installed at the rear end of the X-axis screw rod; the abrasive belt grinding head includes a polishing frame plate, a machine head seat, an abrasive belt mechanism and a Z-direction feed mechanism , the polished shelf includes two side shelves and a top shelf, the two side shelves are installed on both sides of the frame base, the top shelf is installed on the top of the side shelf, and the inner side of the side shelf is equipped with a Z To the feed mechanism, wherein the Z-direction feed mechanism in this embodiment is the screw installation mechanism d...
PUM
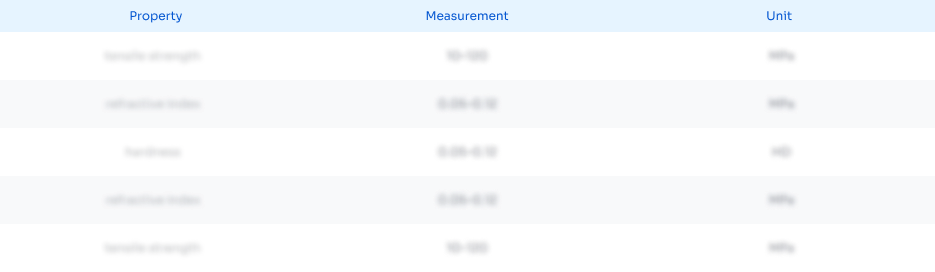
Abstract
Description
Claims
Application Information

- R&D Engineer
- R&D Manager
- IP Professional
- Industry Leading Data Capabilities
- Powerful AI technology
- Patent DNA Extraction
Browse by: Latest US Patents, China's latest patents, Technical Efficacy Thesaurus, Application Domain, Technology Topic, Popular Technical Reports.
© 2024 PatSnap. All rights reserved.Legal|Privacy policy|Modern Slavery Act Transparency Statement|Sitemap|About US| Contact US: help@patsnap.com