Method and device for recycling oily sludge of iron and steel plant
A technology for iron and steel plants and resource utilization, which is applied in chemical instruments and methods, sludge treatment, pyrolysis treatment of sludge, etc. large problems, to achieve the effect of short processing time, fast heating speed and large cross-sectional area
- Summary
- Abstract
- Description
- Claims
- Application Information
AI Technical Summary
Problems solved by technology
Method used
Image
Examples
Embodiment 1
[0106] In this example, the steel plant is hot-rolled as an example, and its physical properties are shown in Table 1.
[0107] Table 1 Oil-containing sewage characteristics
[0108] name Water content,% Oil content,% Heap density, g / cm 3
Oil-containing iron oxide 9.32 1.98 2.50 Hot rolled oil-containing sludge 5.19 10.97 1.02
[0109] The oil-containing mud was added to the storage bin, and 6% lime was mixed after the strand, mix well, granulated.
[0110] Start the molten salt heating system and pyrolysis flue gas treatment system, liquid molten salt in the spiral heating kiln jacket flows for 5-10 min, then start the spiral feeder and the migrant of each spiral kiln, and increase the melting salt heating furnace The blast furnace gas volume allows the exit molten salt temperature of the molten salt heating furnace to 500 ° C.
[0111] Start the turbine rotary trolley and microwave heating electronics control system, and oil-containing mud is p...
Embodiment 2
[0119] In this example, the steel plant is hot-rolled as an example, and its physical properties are shown in Table 1.
[0120] The oil-containing mud was added to the storage bin, and 5% lime was blended after the strand, mix well, granulated.
[0121] Start the molten salt heating system and pyrolysis flue gas treatment system, liquid molten salt in the spiral heating kiln jacket flows for 5-10 min, then start the spiral feeder and the migrant of each spiral kiln, and increase the melting salt heating furnace The blast furnace gas volume allows the exit molten salt temperature of the molten salt heating furnace to 500 ° C.
[0122] Start the bottom furnace rotary trolley and microwave heating electric control system, the oil-containing mud is preheated by the first paragraph to the third spiral kiln, and the temperature of the sludge reaches 380 ° C into the microwave turning bottom.
[0123] The power of the rotational speed and microwave of the rotary trolley is controlled, so...
Embodiment 3
[0131] In this example, the steel plant is hot-rolled as an example, and its physical properties are shown in Table 1.
[0132] The oil-containing mud was added to the storage bin, and 4% lime was mixed after the strand, mix well, granulated. Start the molten salt heating system and pyrolysis flue gas treatment system, liquid molten salt in the spiral heating kiln jacket flows for 5-10 min, then start the spiral feeder and the migrant of each spiral kiln, and increase the melting salt heating furnace The blast furnace gas volume allows the exit molten salt temperature of the molten salt heating furnace to 500 ° C.
[0133] Start the bottom furnace rotary trolley and microwave heating electric control system, the oil-containing mud is preheated by the first paragraph to the third spiral kiln, and the temperature of the sludge reaches 400 ° C and enters the microwave turning bottom, control the bottom The speed of rotational speed and microwave of the furnace rotates, so that the sl...
PUM
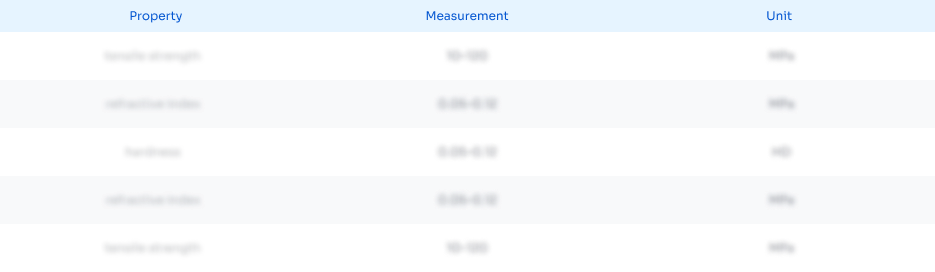
Abstract
Description
Claims
Application Information

- Generate Ideas
- Intellectual Property
- Life Sciences
- Materials
- Tech Scout
- Unparalleled Data Quality
- Higher Quality Content
- 60% Fewer Hallucinations
Browse by: Latest US Patents, China's latest patents, Technical Efficacy Thesaurus, Application Domain, Technology Topic, Popular Technical Reports.
© 2025 PatSnap. All rights reserved.Legal|Privacy policy|Modern Slavery Act Transparency Statement|Sitemap|About US| Contact US: help@patsnap.com