Antibacterial wear-resistant glaze and preparation method thereof
A substance, zircon technology, applied in the field of sanitary ware, can solve the problems of glaze layer wear and poor adhesion between the glaze layer and the ceramic body, and achieve the effect of improving adhesion
- Summary
- Abstract
- Description
- Claims
- Application Information
AI Technical Summary
Problems solved by technology
Method used
Image
Examples
Embodiment 1
[0025] (1) Get 400kg of zircon, 45kg of willemite, 90kg of white clay, 135kg of talcum powder, 405kg of marble, 1095kg of feldspar, 840kg of quartz stone and 63kg of monazite, put them into a ball mill jar and grind to 200 mesh, and set aside; take zirconium Stone 470kg, spodumene 170kg, willemite 100kg, clay 850kg, feldspar 730kg, quartz stone 710kg, bile alum 200kg, perovskite 370kg, edible glue 300kg and cuprous oxide 55kg, put into the ball mill jar, grind to 300 mesh, spare;
[0026] (2) Take the ground first component obtained in step (1) and add 1000 kg of water, stir for 3 hours to obtain a slurry;
[0027] (3) Soak the ceramic green body in the slurry obtained in step (2), and dry naturally;
[0028] (4) Calcining the naturally dried ceramic body is as follows: heat up to 400°C and stay for 3 hours, then heat up to 820°C and stay for 4 hours, then heat up to 1300°C and stay for 4 hours, take it out, and wait for natural cooling before use;
[0029] (5) Take the grou...
Embodiment 2
[0032] (1) Take 370kg of zircon, 50kg of willemite, 100kg of white clay, 140kg of talcum powder, 350kg of marble, 1000kg of feldspar, 800kg of quartz stone and 50kg of monazite, put them into a ball mill jar and grind to 220 mesh, and set aside; take zirconium Stone 560kg, spodumene 200kg, willemite 80kg, clay 800kg, feldspar 680kg, quartz stone 790kg, bile alum 300kg, perovskite 300kg, edible glue 400kg and cuprous oxide 40kg, put into the ball mill jar, grind to 360 mesh, spare;
[0033] (2) Take the ground first component obtained in step (1) and add 1000 kg of water, stir for 2 hours to obtain a slurry;
[0034] (3) Soak the ceramic green body in the slurry obtained in step (2), and dry naturally;
[0035] (4) Calcining the naturally dried ceramic body, specifically: raising the temperature to 500°C for 2 hours, then raising the temperature to 900°C for 4 hours, then raising the temperature to 1380°C for 3 hours, taking it out, and waiting for natural cooling before use; ...
Embodiment 3
[0039] (1) Get 430kg of zircon, 40kg of willemite, 80kg of white clay, 120kg of talcum powder, 430kg of marble, 1200kg of feldspar, 900kg of quartz stone and 70kg of monazite, put them into a ball mill jar and grind to 220 mesh, and set aside; take zirconium Stone 420kg, spodumene 100kg, willemite 120kg, clay 920kg, feldspar 830kg, quartz stone 790kg, bile alum 300kg, perovskite 470kg, edible glue 200kg and cuprous oxide 70kg, put into the ball mill jar, grind to 300 mesh, spare;
[0040] (2) Take the ground first component obtained in step (1) and add 1000 kg of water, stir for 2 hours to obtain a slurry;
[0041] (3) Soak the ceramic green body in the slurry obtained in step (2), and dry naturally;
[0042] (4) Calcining the naturally dried ceramic body, specifically: raising the temperature to 500°C for 2 hours, then raising the temperature to 900°C for 4 hours, then raising the temperature to 1260°C for 5 hours, taking it out, and waiting for natural cooling before use; ...
PUM
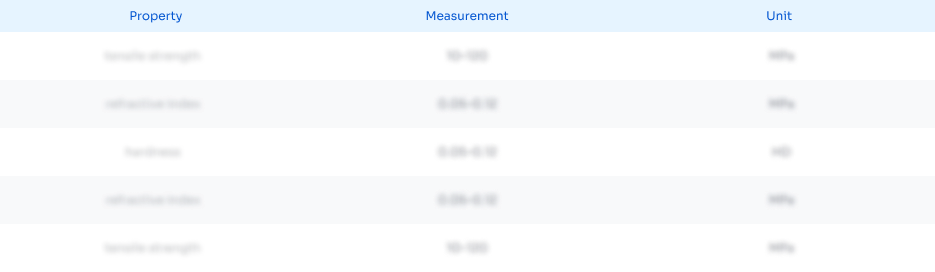
Abstract
Description
Claims
Application Information

- R&D
- Intellectual Property
- Life Sciences
- Materials
- Tech Scout
- Unparalleled Data Quality
- Higher Quality Content
- 60% Fewer Hallucinations
Browse by: Latest US Patents, China's latest patents, Technical Efficacy Thesaurus, Application Domain, Technology Topic, Popular Technical Reports.
© 2025 PatSnap. All rights reserved.Legal|Privacy policy|Modern Slavery Act Transparency Statement|Sitemap|About US| Contact US: help@patsnap.com