Method for preparing pure sulfuric acid rare earth solution
A rare earth sulfate and solution technology, applied in the direction of improving process efficiency, can solve the problems of high rare earth entrainment and adsorption loss, low solid-liquid reaction efficiency, increased acid and alkali consumption, etc.
- Summary
- Abstract
- Description
- Claims
- Application Information
AI Technical Summary
Problems solved by technology
Method used
Image
Examples
Embodiment 2
[0074] In Examples 25 to 27, the primary leaching solution, primary leaching slag, crystallization mother liquor and rare earth sulfate crystals obtained in Example 2 were used, and the pH at the end point of the secondary leaching for impurity removal was different. In Examples 28 to 30, the primary leaching solution, primary leaching residue, crystallization mother liquor and rare earth sulfate crystals obtained in Example 2 were used, and the depth of impurity removal pH was different.
[0075]
[0076]
[0077]
[0078]
[0079]
[0080]
[0081] In summary, the present invention provides a method for preparing pure sulfuric acid rare earth solution. The present invention utilizes the kinetic characteristics of rare earth dissolution and the characteristics that the solubility of rare earth sulfate decreases with increasing temperature in the sulfuric acid roasted ore leaching process of rare earth, and adopts low liquid-solid ratio Rapid leaching followed...
PUM
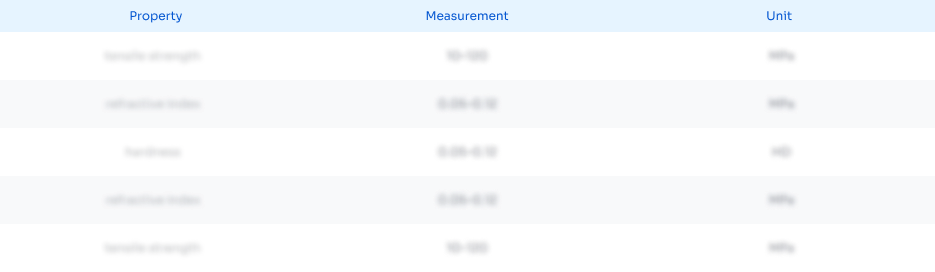
Abstract
Description
Claims
Application Information

- R&D
- Intellectual Property
- Life Sciences
- Materials
- Tech Scout
- Unparalleled Data Quality
- Higher Quality Content
- 60% Fewer Hallucinations
Browse by: Latest US Patents, China's latest patents, Technical Efficacy Thesaurus, Application Domain, Technology Topic, Popular Technical Reports.
© 2025 PatSnap. All rights reserved.Legal|Privacy policy|Modern Slavery Act Transparency Statement|Sitemap|About US| Contact US: help@patsnap.com