Antibacterial wear-resistant runway floor composite material and preparation method thereof
A composite material and flooring technology, applied in the direction of additive processing, etc., can solve the problems of insufficient wear resistance and runway application requirements, poor cold resistance, etc., to improve antibacterial sterilization and decontamination self-cleaning, inhibit composite, The effect of improving photogenerated quantum efficiency
- Summary
- Abstract
- Description
- Claims
- Application Information
AI Technical Summary
Problems solved by technology
Method used
Image
Examples
Embodiment 1
[0051]First add 0.5 parts by weight of UV stabilizer, 0.4 parts by weight of antioxidant and 20 parts by weight of reinforcing agent into a high-speed mixer and mix at room temperature for 10 minutes until evenly mixed, then add 0.2 parts by weight of antibacterial composite microspheres into the mixture and mix for 10 minutes at room temperature Mix until uniform to obtain mixture A, set aside; then add 71.9 parts by weight of matrix material and 3 parts by weight of dispersant to a high-speed mixer and mix for 5 minutes at room temperature until uniform, then add 4 parts by weight of crosslinking agent, and set the temperature to 50°C , mixed for 10 minutes until uniform, to obtain mixture B; finally, add mixture A to mixture B, keep the temperature at 50°C, and mix for 20 minutes to obtain a mixed material;
[0052] Then add the mixed material into the twin-screw for melt mixing extrusion and pelletizing. The temperature setting is: 155°C for the first stage, 165°C for the s...
Embodiment 2
[0055] First, add 1 part by weight of UV stabilizer, 0.4 parts by weight of antioxidant and 20 parts by weight of reinforcing agent into a high-speed mixer and mix at room temperature for 10 minutes until uniformly mixed, then add 0.2 parts by weight of antibacterial composite microspheres into the mixture and mix for 10 minutes at room temperature Mix until uniform to obtain mixture A, set aside; then add 71.2 parts by weight of matrix material and 3 parts by weight of dispersant to a high-speed mixer and mix for 5 minutes at room temperature until uniform, then add 4 parts by weight of crosslinking agent, and set the temperature to 50°C , mixed for 10 minutes until uniform, to obtain mixture B; finally, add mixture A to mixture B, keep the temperature at 50°C, and mix for 20 minutes to obtain a mixed material;
[0056] Then add the mixed material into the twin-screw for melt mixing extrusion and pelletizing. The temperature setting is: 155°C for the first stage, 165°C for the...
Embodiment 3
[0059] First add 1.5 parts by weight of UV stabilizer, 0.4 parts by weight of antioxidant and 20 parts by weight of reinforcing agent into a high-speed mixer and mix at room temperature for 10 minutes until uniformly mixed, then add 0.6 parts by weight of antibacterial composite microspheres into the mixture and mix for 10 minutes at room temperature Mix until uniform to obtain mixture A, set aside; then add 70.5 parts by weight of matrix material and 3 parts by weight of dispersant to a high-speed mixer and mix for 5 minutes at room temperature until uniform, then add 4 parts by weight of crosslinking agent, and set the temperature to 50°C , mixed for 10 minutes until uniform, to obtain mixture B; finally, add mixture A to mixture B, keep the temperature at 50°C, and mix for 20 minutes to obtain a mixed material;
[0060] Then add the mixed material into the twin-screw for melt mixing extrusion and pelletizing. The temperature setting is: 155°C for the first stage, 165°C for t...
PUM
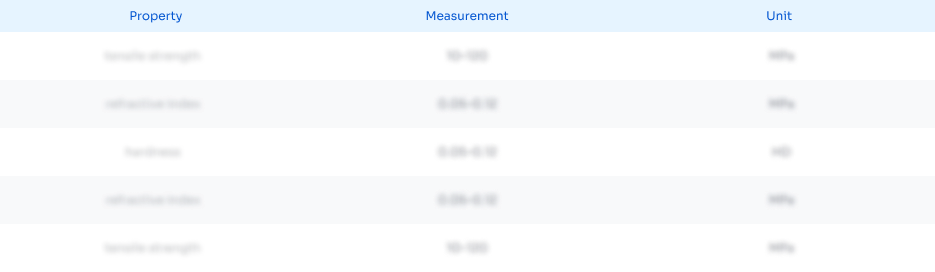
Abstract
Description
Claims
Application Information

- R&D
- Intellectual Property
- Life Sciences
- Materials
- Tech Scout
- Unparalleled Data Quality
- Higher Quality Content
- 60% Fewer Hallucinations
Browse by: Latest US Patents, China's latest patents, Technical Efficacy Thesaurus, Application Domain, Technology Topic, Popular Technical Reports.
© 2025 PatSnap. All rights reserved.Legal|Privacy policy|Modern Slavery Act Transparency Statement|Sitemap|About US| Contact US: help@patsnap.com