Large-core-diameter plastic side face light emitting optical fiber and optical cable manufacturing device
A technology for manufacturing equipment and side-light optical fibers, which is applied in the direction of optical fiber light guides, clad optical fibers, and optical waveguide light guides. Difficult optical fiber and other problems, to achieve the effect of good light guiding performance
- Summary
- Abstract
- Description
- Claims
- Application Information
AI Technical Summary
Problems solved by technology
Method used
Image
Examples
preparation example Construction
[0107] see Figure 8 The embodiment of the present invention also provides a method for preparing a large-core polymer side-firing optical fiber, which is applicable to the manufacturing equipment for the large-core polymer side-firing optical fiber provided in any embodiment of the present invention. Such as Figure 8 Said, the method includes the following steps:
[0108] Step 810, mix the core layer material uniformly and perform high-temperature treatment to make the core layer material into a molten state, wherein the core layer material includes the first polymer and the first scattering particles;
[0109] In this embodiment, the temperature of the core material extruder is raised to the first preset temperature, and after the core material is evenly mixed by the first stirring device, the core material is input into the screw barrel of the core material extruder , the core layer material is plasticized and mixed evenly through the pressure and shear force generated b...
PUM
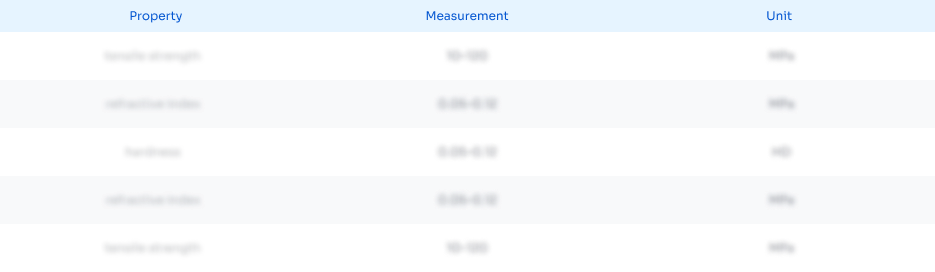
Abstract
Description
Claims
Application Information

- R&D Engineer
- R&D Manager
- IP Professional
- Industry Leading Data Capabilities
- Powerful AI technology
- Patent DNA Extraction
Browse by: Latest US Patents, China's latest patents, Technical Efficacy Thesaurus, Application Domain, Technology Topic, Popular Technical Reports.
© 2024 PatSnap. All rights reserved.Legal|Privacy policy|Modern Slavery Act Transparency Statement|Sitemap|About US| Contact US: help@patsnap.com