Movable robot based on paper folding structure and snake-like robot
A mobile robot and origami structure technology, applied in the field of robotics, can solve the problems of reliability and payload limitation, system complexity, volume and weight increase, etc., and achieve the effect of light weight, large payload ratio and high driving efficiency
- Summary
- Abstract
- Description
- Claims
- Application Information
AI Technical Summary
Problems solved by technology
Method used
Image
Examples
Embodiment 1
[0042] The embodiment according to the present embodiment figure 1 As shown by the two motion module and a front load module 1, module 2 is composed of the load.
[0043] One end of the motion module load module, and the other end connected to the intermediate partition. Micro servo drive or a shape memory alloy folded tube disposed within the rotary drive load module.
[0044] Two unidirectional load module is installed outside the roller 6, when the load module is moved forward, the unidirectional roller 6 can be rotated between the ground and with less resistance. When the load module is retracted, the one-way roller 6 against rotation, between the ground and having a large frictional resistance.
[0045] Specifically run, one forward motion of the joint cycle of two steps:
[0046]1) First step: The micro-servo or shape memory alloy rotation drive drives the Kresling tube within the two motion modules while shrinking. At this time, the previous load module 1 has a trend of bac...
Embodiment 2
[0054] In this embodiment, it consists of 1 moving module and the front, the rear load module, such as Figure 5 Indicated. One end of the motion module is connected to the previous load module 1, and the other end is connected to the rear load module 2. The micro-servulator or shape memory alloy rotation drive of the Kresling folding tube is placed in one of the load modules or within the front and rear load modules. The two sets of unidirectional rollers 6 are mounted outside the load module. When the load module moves forward, the one-way roller 6 can be rotated, and the resistance between the ground is smaller. When the load module is retired, the one-way roller 6 cannot rotate, and there is a large friction resistance between the ground.
[0055] One advance cycle of the exercise joint is divided into two steps:
[0056] 1) First step: The micro-servo is simultaneously contracted by the Kresling tube in which the micro-servo or shape memory alloy rotates the driving of the mot...
Embodiment 3
[0064] If the motion module uses 4 90 ° intervals of Kresling folding tubes, such as image 3 with Figure 4 As shown, the motion module can be changed as long as the two orthogonal planes, so that the moving robots in the present embodiments 1 and 2 can be made not only to bend during the forward process, but also pitch. It is conducive to overdraws and passed.
PUM
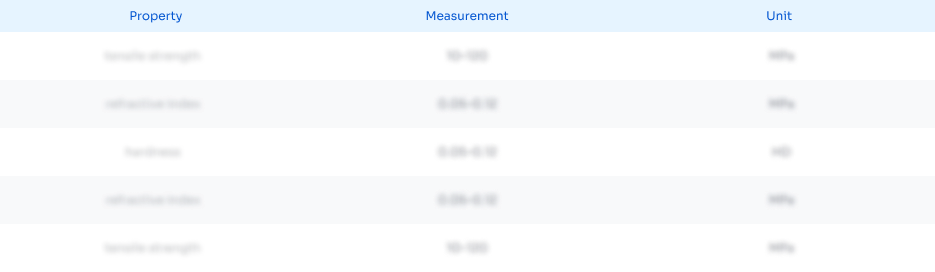
Abstract
Description
Claims
Application Information

- R&D Engineer
- R&D Manager
- IP Professional
- Industry Leading Data Capabilities
- Powerful AI technology
- Patent DNA Extraction
Browse by: Latest US Patents, China's latest patents, Technical Efficacy Thesaurus, Application Domain, Technology Topic, Popular Technical Reports.
© 2024 PatSnap. All rights reserved.Legal|Privacy policy|Modern Slavery Act Transparency Statement|Sitemap|About US| Contact US: help@patsnap.com