Ceramic tile glaze raw material and preparation method thereof
A technology for glazed surface and tiles, which is applied in the field of glazed raw material formula and its preparation process, which can solve the problems of the overall quality decline of glazed surface materials, large glaze loss on ignition, and different sizes, so as to improve the bonding performance of blank glaze and improve Effect of antifouling performance and good mechanical strength
- Summary
- Abstract
- Description
- Claims
- Application Information
AI Technical Summary
Problems solved by technology
Method used
Examples
Embodiment 1
[0027] Raw material ball milling: firstly weigh the components of the ceramic tile glaze raw material according to the proportion by weight, 60 parts of kaolin, 13 parts of calcite, 4 parts of barium carbonate, 18 parts of clay, 3 parts of titanium dioxide powder, 2 parts of wollastonite, 3 parts of limestone 6 parts, 6 parts of feldspar, 3 parts of quartz sand, 4 parts of diopside, 2 parts of sodium carboxymethyl cellulose, 3 parts of sodium tripolyphosphate, 7 parts of borax, then add the ceramic tile glaze raw material into a ball mill for ball milling Operation, the composition of the ceramic tile glaze raw material: the ratio of water: ball is 1:1.2:1.8, and the glaze raw slurry is obtained after the completion; the processing fineness of the ceramic tile glaze raw material is 200 mesh;
[0028] Calcination of glazed raw slurry: Put the glazed raw slurry into a dryer for drying, the water content is 6.5%, and then use a press to press the glazed raw slurry into long bricks...
Embodiment 2
[0031] First, weigh the components of the ceramic tile glaze raw material in parts by weight. In terms of parts by weight, the components of the ceramic tile glaze raw material include: 58 parts of kaolin, 16 parts of calcite, 3 parts of barium carbonate, and 16 parts of clay. 3 parts of titanium dioxide powder, 1 part of wollastonite, 3 parts of limestone, 5 parts of feldspar, 2 parts of quartz sand, 4 parts of diopside, 2 parts of sodium carboxymethyl cellulose, 3 parts of sodium tripolyphosphate, borax 5 parts, then add the ceramic tile glaze raw material into a ball mill for ball milling, the composition of the ceramic tile glaze raw material: water: the ratio of balls is 1:1:1.6, and the glaze raw slurry is obtained after the end; The processing fineness of ceramic tile glaze raw materials is 250 mesh;
[0032] Calcination of glazed raw slurry: Put the glazed raw slurry into the dryer for drying, the water content is 8%, and then use the press to press the glazed raw slur...
PUM
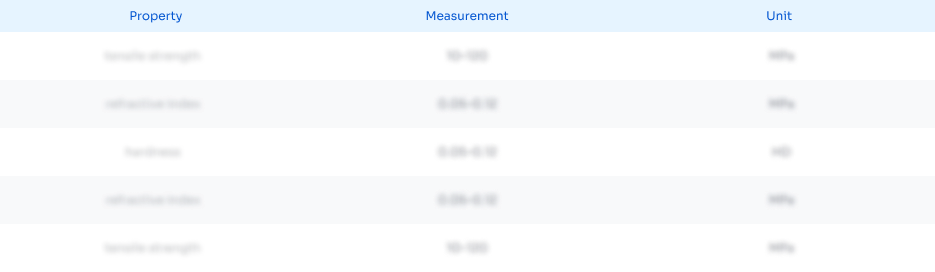
Abstract
Description
Claims
Application Information

- R&D
- Intellectual Property
- Life Sciences
- Materials
- Tech Scout
- Unparalleled Data Quality
- Higher Quality Content
- 60% Fewer Hallucinations
Browse by: Latest US Patents, China's latest patents, Technical Efficacy Thesaurus, Application Domain, Technology Topic, Popular Technical Reports.
© 2025 PatSnap. All rights reserved.Legal|Privacy policy|Modern Slavery Act Transparency Statement|Sitemap|About US| Contact US: help@patsnap.com