Preparation method for producing cupronickel B30 raw material from copper-nickel slag
A technology of copper-nickel slag and B30, applied in the field of smelting, can solve the problems of incomplete homogenization of elements such as copper-nickel-iron and high cost, and achieve significant environmental protection benefits and low investment
- Summary
- Abstract
- Description
- Claims
- Application Information
AI Technical Summary
Problems solved by technology
Method used
Image
Examples
preparation example Construction
[0020] A kind of copper-nickel slag produces the preparation method of cupronickel B30 raw material, and its technological process is:
[0021] a. Crush the copper-nickel slag material to about 50mm, and the water content after drying is less than 10%;
[0022] b. Mix the dried copper-nickel slag material, reducing agent and flux in proportion and then add them to the DC electric arc furnace;
[0023] c. Control the temperature of the DC electric arc furnace at 1380°C-1500°C, the feeding time is 30-60 minutes, the holding time is 30-60 minutes, and the slag and copper-nickel alloy are separated;
[0024] d. Copper-nickel alloy is desulfurized, decarburized, and impurity-removed through AOD furnace and other equipment to prepare qualified white copper B30 raw materials.
[0025] Further, the amount of the reducing agent added in step b is 5-7.5% of the copper-nickel slag on a dry basis.
[0026] Further, the amount of flux added in step b is 13-15% of the dry copper-nickel sl...
Embodiment 1
[0031] First, after the copper-nickel slag is naturally dried, its water content is less than 10%, and a certain amount of dry base copper-nickel slag is weighed, and the reducing agent is weighed according to 5% of the copper-nickel slag amount, and the auxiliary agent is weighed according to 13% of the copper-nickel slag amount. Flux: All materials are weighed and mixed in a small amount and added to the hot DC electric arc furnace in batches. The melting temperature of the DC electric arc furnace is controlled at 1380°C, the feeding time is 30 minutes, and the holding time is 30 minutes. After the holding is completed, the slag and copper-nickel alloy are separated. The copper-nickel alloy is transported to the AOD furnace; the desulfurizer is weighed according to 1% of the alloy amount; the oxygen blowing decarburization, desulfurization by adding the desulfurizer in batches, etc. are refined, after the impurity removal is completed, the casting is carried out, and the chemi...
Embodiment 2
[0035] First, after the copper-nickel slag is naturally dried, its water content is less than 10%, and a certain amount of dry base copper-nickel slag is weighed, and the reducing agent is weighed according to 6% of the copper-nickel slag amount, and the auxiliary agent is weighed according to 14% of the copper-nickel slag amount. Flux: All materials are weighed and mixed in a small amount and added to the hot DC electric arc furnace in batches. The melting temperature of the DC electric arc furnace is controlled at 1450°C, the feeding time is 50 minutes, and the holding time is 50 minutes. After the holding, the slag and copper-nickel alloy are separated. The copper-nickel alloy is transported to the AOD furnace; the desulfurization agent is weighed according to 1% of the alloy amount; oxygen blowing decarburization, adding desulfurization agent in batches for desulfurization and other refining, casting after impurity removal, cooling sampling chemical composition analysis, the...
PUM
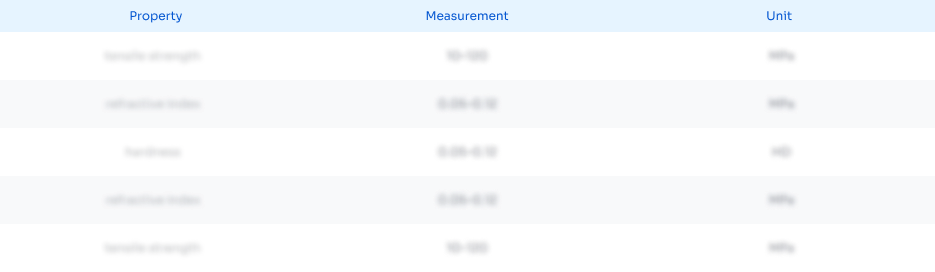
Abstract
Description
Claims
Application Information

- R&D
- Intellectual Property
- Life Sciences
- Materials
- Tech Scout
- Unparalleled Data Quality
- Higher Quality Content
- 60% Fewer Hallucinations
Browse by: Latest US Patents, China's latest patents, Technical Efficacy Thesaurus, Application Domain, Technology Topic, Popular Technical Reports.
© 2025 PatSnap. All rights reserved.Legal|Privacy policy|Modern Slavery Act Transparency Statement|Sitemap|About US| Contact US: help@patsnap.com