Magnesium/aluminum alloy composite material and preparation process thereof
A composite material and preparation technology, which is applied in the coating process of metal materials, manufacturing tools, metal rolling, etc., can solve the problem that the lightweight of composite materials cannot meet the requirements, so as to improve the physical fitting point, improve the bonding strength, and achieve compactness. sex high effect
- Summary
- Abstract
- Description
- Claims
- Application Information
AI Technical Summary
Problems solved by technology
Method used
Image
Examples
Embodiment 1
[0036] In this example, 5052 aluminum alloy and AZ31 magnesium alloy plate are selected for composite. The AZ31 magnesium alloy plate of 10×200×300mm is subjected to plasma spraying treatment on one side. The first 25μm coating is sprayed with a power of 38kW, the spray distance is 115mm, and the main air flow is 40L / min; the last 35μm coating is sprayed with a power of 40kW and spray The spraying process with a distance of 100mm and a main air flow rate of 40L / min sprays a layer of 60um thick pure aluminum on the surface; sandblasts the surface of the 5052 alloy plate of 5×200×300mm to remove impurities and oil stains on the surface of the plate. The processed magnesium alloy plate and aluminum alloy plate are riveted together with 5052 aluminum alloy. Put the riveted plate into a heating furnace and keep it warm at 360°C for 1h. Carry out hot rolling, the reduction is 50%, and the rolling speed is 8m / min. After the first hot rolling, the plate is kept at 360°C for 15 minute...
Embodiment 2
[0038]In this example, 5052 aluminum alloy and AZ42 magnesium alloy plate are selected for composite. One side of the 10×200×300mm AZ42 magnesium alloy plate is subjected to plasma spraying treatment. The first 30μm coating is sprayed with a power of 40kW, the spraying distance is 120mm, and the main air flow is 40L / min; the last 40μm coating is sprayed with a power of 40kW and The spraying process with a distance of 110mm and a main air flow rate of 40L / min sprays a layer of 70um thick pure aluminum on the surface; the surface of the 5052 alloy plate of 5×200×300mm is sandblasted to remove impurities and oil stains on the surface. The processed magnesium alloy plate and aluminum alloy plate are riveted together with 5052 aluminum alloy. Put the riveted sheet into a heating furnace and keep it at 400°C for 1 hour; carry out hot rolling with a reduction of 60% and a rolling speed of 12m / min. After the first hot-rolled sheet is held at 400°C for 15 minutes , Carry out the secon...
Embodiment 3
[0040] In this example, 5052 aluminum alloy and AZ31 magnesium alloy plate are selected for composite. One side of the 20×200×200mm AZ31 magnesium alloy plate is subjected to plasma spraying treatment, the first 25μm coating is sprayed with a power of 40kW, the spraying distance is 125mm, and the main air flow is 40L / min; the last 35μm coating is sprayed with a power of 40kW, The spraying process with a distance of 105mm and a main air flow rate of 40L / min sprays a layer of 60um thick pure aluminum on the surface; sandblasting the surface of the 5052 alloy plate of 10×200×200mm to remove impurities and oil stains on the surface. The processed magnesium alloy plate and aluminum alloy plate are riveted together with 5052 aluminum alloy. Put the riveted plate into a heating furnace and keep it warm at 420°C for 1 hour; carry out hot rolling with a reduction of 75% and a rolling speed of 10m / min to a thickness of about 7.5mm. Thermal diffusion annealing was performed at 260°C for...
PUM
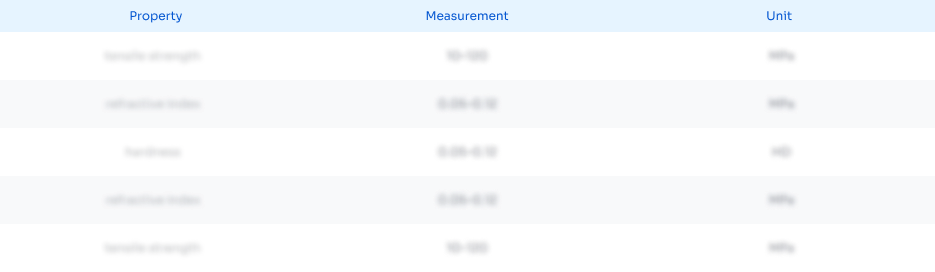
Abstract
Description
Claims
Application Information

- Generate Ideas
- Intellectual Property
- Life Sciences
- Materials
- Tech Scout
- Unparalleled Data Quality
- Higher Quality Content
- 60% Fewer Hallucinations
Browse by: Latest US Patents, China's latest patents, Technical Efficacy Thesaurus, Application Domain, Technology Topic, Popular Technical Reports.
© 2025 PatSnap. All rights reserved.Legal|Privacy policy|Modern Slavery Act Transparency Statement|Sitemap|About US| Contact US: help@patsnap.com