Water-based plastic absorbing adhesive and preparation method thereof
A plastic and water-based technology, applied in the field of water-based absorbent plastic and its preparation, can solve the problem that the water-based absorbent plastic cannot meet the needs of use, and achieve the effects of good anti-adhesion resistance, good mechanical strength, and improved compatibility.
- Summary
- Abstract
- Description
- Claims
- Application Information
AI Technical Summary
Problems solved by technology
Method used
Examples
Embodiment 1
[0026] A preparation method for water-based plastic absorbing plastic, comprising the steps of:
[0027] (1) Synthesis of hydroxyethyl acrylate-vinyl acetate copolymer: Weigh vinyl acetate, hydroxyethyl acrylate and initiator for mixing, heat up to 75°C, and react for 1.5h to obtain hydroxyethyl acrylate-vinyl acetate Ester copolymer, the mass ratio of described vinyl acetate and hydroxyethyl acrylate is 75:25, and the quality of initiator is 0.3% of the mass sum of vinyl acetate and hydroxyethyl acrylate;
[0028] (2) Synthesis of polyurethane acrylate: take by weight 16.5% of diisocyanate, 9% of polyester polyol, 11.5% of hydroxyethyl acrylate-vinyl acetate copolymer of step (1), 2% of chain extender, Catalyst 0.05%, neutralizer 1.5%, defoamer 0.2% and water balance, add diisocyanate, polyester polyol and catalyst in the reaction kettle, raise the temperature to 85°C and react for 2.5h, then add hydroxyethyl acrylate- Vinyl acetate copolymer, continue to keep warm for 2.5 h...
Embodiment 2
[0039] A preparation method for water-based plastic absorbing plastic, comprising the steps of:
[0040] (1) Synthesis of hydroxyethyl acrylate-vinyl acetate copolymer: weigh vinyl acetate, hydroxyethyl acrylate and initiator for mixing, heat up to 70°C, and react for 1 hour to obtain hydroxyethyl acrylate-vinyl acetate Copolymer, the mass ratio of described vinyl acetate and hydroxyethyl acrylate is 70:30, and the quality of initiator is 0.1% of the mass sum of vinyl acetate and hydroxyethyl acrylate;
[0041](2) Synthesis of polyurethane acrylate: take by weight 15% of diisocyanate, 8% of polyester polyol, 10% of hydroxyethyl acrylate-vinyl acetate copolymer of step (1), 1% of chain extender, Catalyst 0.01%, neutralizer 1%, defoamer 0.1% and water balance, add diisocyanate, polyester polyol and catalyst in the reaction kettle, heat up to 80°C and react for 2h, then add hydroxyethyl acrylate-acetic acid Vinyl ester copolymer, continue to keep warm for 2h, cool down to 60°C a...
Embodiment 3
[0052] A preparation method for water-based plastic absorbing plastic, comprising the steps of:
[0053] (1) Synthesis of hydroxyethyl acrylate-vinyl acetate copolymer: weigh vinyl acetate, hydroxyethyl acrylate and initiator for mixing, heat up to 80°C, and react for 2 hours to obtain hydroxyethyl acrylate-vinyl acetate Copolymer, the mass ratio of described vinyl acetate and hydroxyethyl acrylate is 80:20, and the quality of initiator is 0.5% of the mass sum of vinyl acetate and hydroxyethyl acrylate;
[0054] (2) Synthesis of polyurethane acrylate: take by mass percentage 18% of diisocyanate, polyester polyol 10%, 13% of hydroxyethyl acrylate-vinyl acetate copolymer of step (1), 3% of chain extender, Catalyst 0.1%, neutralizer 2%, defoamer 0.3% and water balance, add diisocyanate, polyester polyol and catalyst in the reaction kettle, raise the temperature to 90°C and react for 3h, then add hydroxyethyl acrylate-acetic acid Vinyl ester copolymer, continue to keep warm for 3...
PUM
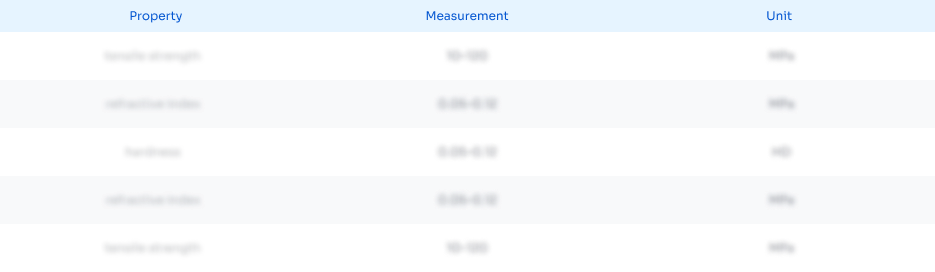
Abstract
Description
Claims
Application Information

- Generate Ideas
- Intellectual Property
- Life Sciences
- Materials
- Tech Scout
- Unparalleled Data Quality
- Higher Quality Content
- 60% Fewer Hallucinations
Browse by: Latest US Patents, China's latest patents, Technical Efficacy Thesaurus, Application Domain, Technology Topic, Popular Technical Reports.
© 2025 PatSnap. All rights reserved.Legal|Privacy policy|Modern Slavery Act Transparency Statement|Sitemap|About US| Contact US: help@patsnap.com