Surfactant-added composite modified anti-corrosion zinc-rich coating and preparation method thereof
A surfactant and composite modification technology, applied in anti-corrosion coatings, epoxy resin coatings, coatings, etc., can solve the problems of poor anti-settling, difficult construction of coatings, easy agglomeration, etc., to improve mechanical properties and anti-corrosion properties, Effects of improved dispersibility and corrosion resistance, and reduced self-corrosion current density
- Summary
- Abstract
- Description
- Claims
- Application Information
AI Technical Summary
Problems solved by technology
Method used
Examples
preparation example Construction
[0023] The present invention also provides a method for preparing a composite modified anti-corrosion zinc-rich coating, comprising the following steps:
[0024] S1. Raw material preparation: each component is weighed according to the parts by weight of the composite modified anti-corrosion zinc-rich coating added with the above-mentioned surfactant.
[0025] S2. Pour the epoxy resin and the polyamide into a reaction device, heat and stir to obtain a first mixed liquid.
[0026] Further, in a preferred embodiment of the present invention, the heating temperature is 30-40° C., and the stirring time is 10-20 minutes. Preferably, the stirring time is 15 minutes.
[0027] S3. Pour the curing agent, the leveling agent, the toughening agent, the degassing agent and the flow promoter into the first mixed liquid, heat and stir to obtain a second mixed liquid .
[0028] Further, in a preferred embodiment of the present invention, the heating temperature is 50-70° C., and the stirrin...
Embodiment 1
[0037] A kind of composite modified anticorrosion zinc-rich coating that adds surfactant provided in this embodiment, by weight, includes 20 parts of epoxy resin, 10 parts of polyamide, 5 parts of curing agent, 5 parts of leveling agent, 0.5 parts of Part toughening agent, 0.1 part degassing agent, 0.1 part flow promoter, 5 parts potassium silicate solution, 20 parts zinc powder and 5 parts filler.
[0038] A method for preparing a composite modified anti-corrosion zinc-rich paint, comprising the following steps:
[0039] S1. Raw material preparation: measure the required weight of each component of the composite modified anti-corrosion zinc-rich coating respectively by weighing equipment.
[0040] S2. Pour the epoxy resin and polyamide into the reaction device, and stir at 40° C. for 15 minutes to obtain the first mixed solution.
[0041] S3. Pour the curing agent, leveling agent, toughening agent, degasser and flow promoter into the first mixed liquid, and stir at 50° C. fo...
Embodiment 2
[0045] A kind of composite modified anticorrosion zinc-rich coating that adds surfactant provided in this embodiment, comprises 40 parts of epoxy resins, 30 parts of polyamides, 10 parts of curing agents, 15 parts of leveling agents, 1 part by weight. Part toughening agent, 0.5 part degassing agent, 0.6 part flow promoter, 15 parts potassium silicate solution, 50 parts zinc powder and 20 parts filler.
[0046] A method for preparing a composite modified anti-corrosion zinc-rich paint, comprising the following steps:
[0047] S1. Raw material preparation: measure the required weight of each component of the composite modified anti-corrosion zinc-rich coating respectively by weighing equipment.
[0048] S2. Pour the epoxy resin and polyamide into the reaction device, and stir at 30° C. for 15 minutes to obtain the first mixed solution.
[0049] S3. Pour the curing agent, leveling agent, toughening agent, degassing agent and flow promoter into the first mixed liquid, and stir at...
PUM
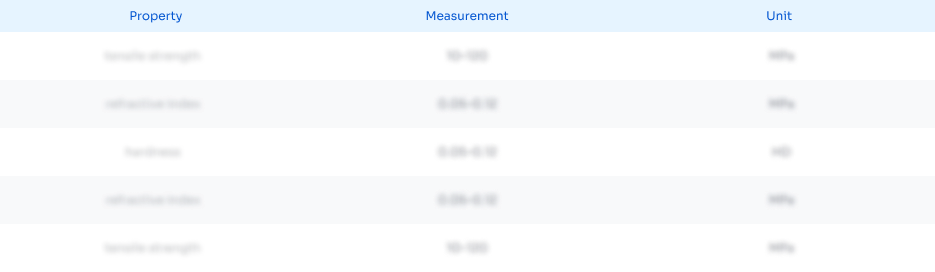
Abstract
Description
Claims
Application Information

- Generate Ideas
- Intellectual Property
- Life Sciences
- Materials
- Tech Scout
- Unparalleled Data Quality
- Higher Quality Content
- 60% Fewer Hallucinations
Browse by: Latest US Patents, China's latest patents, Technical Efficacy Thesaurus, Application Domain, Technology Topic, Popular Technical Reports.
© 2025 PatSnap. All rights reserved.Legal|Privacy policy|Modern Slavery Act Transparency Statement|Sitemap|About US| Contact US: help@patsnap.com