Reinforcing method for loose coal pillar body corrosion-resistant interchange roadway
An anti-corrosion, roadway technology, applied in tunnels, earth-moving drilling, tunnel lining and other directions, can solve the problems of protecting the integrity of the coal column from structural damage, short duration of reinforcement effect, failure of anchor bolt and cable support, etc. The effect of avoiding support failure, reducing environmental protection investment and delaying corrosion time
- Summary
- Abstract
- Description
- Claims
- Application Information
AI Technical Summary
Problems solved by technology
Method used
Image
Examples
Embodiment 1
[0022] see figure 1 , a method for reinforcing a loose coal pillar anti-corrosion interchange roadway, comprising the following steps:
[0023] S1. Construction of the lower roadway 3: set up the I-shaped steel beam support 4 on the roof of the lower roadway 3, use three anchor cables 5 for hoisting, and the distance between the eye positions of the anchor cables 5 is 1800mm, and use the I-shaped steel shed at the same time 6 to lift the I-beam support 4, and the length of the anchor cable 5 on the I-beam support 4 of the lower roadway 3 is greater than the thickness of the coal pillar 2 to be protected;
[0024] S2, spray grout on the roof of the lower roadway 3;
[0025] S3. Construction upper roadway 1: When passing through the overpass area, install I-shaped steel beam support 4 on the exposed anchor cable 5, and use iron drainage pipe 7 to replace the cement ditch, and at the same time support the I-shaped steel beam 4 Lay waterproof material on the upper part and pour ...
Embodiment 2
[0032] Embodiment two differs from embodiment one in that:
[0033] In this embodiment, the waterproof material also includes P.O32.5R composite Portland cement, gangue and pebbles produced from mines.
[0034] The upper roadway 1 is poured by using the gangue produced in the mine instead of the medium-coarse river sand and used with cement. The gangue produced in the underground will not go up the shaft, but will be reused directly in the underground, reducing the processing cost of the gangue in the enterprise after it goes up the shaft. At the same time, the ground environment of the mine is improved, reducing the company's additional investment in environmental protection.
[0035] Others are the same as embodiment one.
[0036] Embodiment 1 and Embodiment 2 are mainly used for support when the mine roadway is buried deep below 800m and exceeds 9m when passing overpasses.
PUM
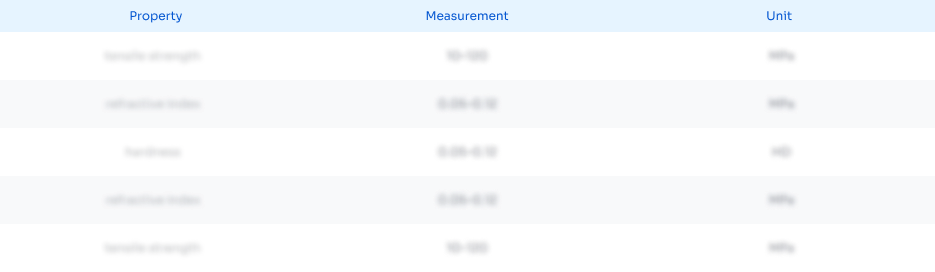
Abstract
Description
Claims
Application Information

- R&D
- Intellectual Property
- Life Sciences
- Materials
- Tech Scout
- Unparalleled Data Quality
- Higher Quality Content
- 60% Fewer Hallucinations
Browse by: Latest US Patents, China's latest patents, Technical Efficacy Thesaurus, Application Domain, Technology Topic, Popular Technical Reports.
© 2025 PatSnap. All rights reserved.Legal|Privacy policy|Modern Slavery Act Transparency Statement|Sitemap|About US| Contact US: help@patsnap.com