Method for comprehensively recovering iron, sulfur and titanium from complex polymetallic ore
A technology for polymetallic ore and iron recovery, applied in the field of sulfur, titanium, and comprehensive iron recovery, which can solve the problems of difficult extraction, little attention to recovery, waste of resources, etc.
- Summary
- Abstract
- Description
- Claims
- Application Information
AI Technical Summary
Problems solved by technology
Method used
Image
Examples
Embodiment 1
[0039] In the complex polymetallic ore used in the present invention, the average iron grade is 13.20%, the sulfur grade is 5.49%, and the titanium grade is 2.96%.
[0040] first step
[0041] A stage of grinding operation is carried out, and the particle size of the fine grinding material is not higher than 0.074mm, accounting for 65%.
[0042] second step
[0043] The ground fine material is subjected to a stage of strong magnetic separation with a magnetic field strength of 960kA / m to obtain a stage of concentrated ore and a stage of tailings.
[0044] A stage of strong magnetic separation concentrate is subjected to a stage of weak magnetic separation, with a magnetic field strength of 400kA / m, to obtain a stage of weak magnetic separation concentrate and a stage of weak magnetic separation tailings. The first-stage weak magnetic separation concentrate is subjected to the second-stage weak magnetic separation concentration, and the magnetic field strength is 300kA / m, and t...
Embodiment 2
[0059] The ore sample used is the ore sample in Example 1.
[0060] first step
[0061] A stage of grinding operation is carried out, and the particle size of the grinding fine material is not higher than 0.074mm, accounting for 62%.
[0062] second step
[0063] The ground fine material is subjected to a stage of strong magnetic separation with a magnetic field strength of 1000kA / m to obtain a stage of concentrated ore and a stage of tailings.
[0064] A stage of strong magnetic separation concentrate is subjected to a stage of weak magnetic separation, with a magnetic field strength of 350kA / m, to obtain a stage of weak magnetic separation concentrate and a stage of weak magnetic separation tailings. The first-stage weak magnetic separation concentrate is subjected to the second-stage weak magnetic separation concentration, and the magnetic field strength is 400kA / m, and the second-stage weak magnetic separation concentrate and the second-stage weak magnetic separation tai...
Embodiment 3
[0079] The mine sample used is the mine sample in Example 1.
[0080] first step
[0081] A stage of grinding operation is carried out, and the particle size of the grinding fine material is not higher than 0.074mm, accounting for 60%.
[0082] second step
[0083] The ground fine material is subjected to a stage of strong magnetic separation with a magnetic field strength of 900kA / m to obtain a stage of concentrated ore and a stage of tailings.
[0084] A stage of strong magnetic separation concentrate is subjected to a stage of weak magnetic separation, with a magnetic field strength of 300kA / m, to obtain a stage of weak magnetic separation concentrate and a stage of weak magnetic separation tailings. The first-stage weak magnetic separation concentrate is subjected to the second-stage weak magnetic separation concentration, and the magnetic field strength is 350kA / m, and the second-stage weak magnetic separation concentrate and the second-stage weak magnetic separation ta...
PUM
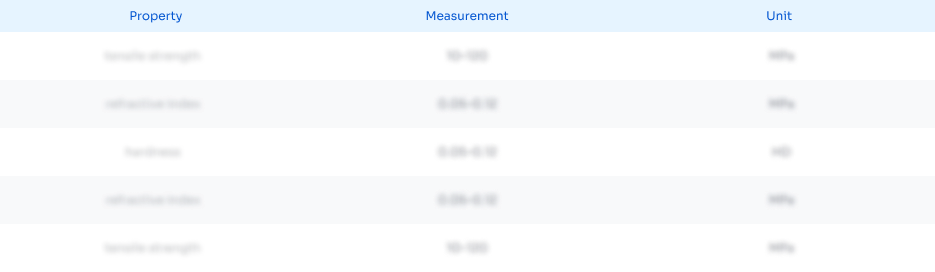
Abstract
Description
Claims
Application Information

- R&D
- Intellectual Property
- Life Sciences
- Materials
- Tech Scout
- Unparalleled Data Quality
- Higher Quality Content
- 60% Fewer Hallucinations
Browse by: Latest US Patents, China's latest patents, Technical Efficacy Thesaurus, Application Domain, Technology Topic, Popular Technical Reports.
© 2025 PatSnap. All rights reserved.Legal|Privacy policy|Modern Slavery Act Transparency Statement|Sitemap|About US| Contact US: help@patsnap.com