Method for preparing heat-conducting preform through heavy oil-waste plastic blending and application of heat-conducting preform
A technology of waste plastics and prefabricated bodies, which is applied in plastic recycling, chemical instruments and methods, heat exchange materials, etc., can solve the problems of complex preparation steps, limit the utilization of high-value resources, and require high equipment conditions, and achieve mature technology, The effect of high applicability and convenient preparation
- Summary
- Abstract
- Description
- Claims
- Application Information
AI Technical Summary
Problems solved by technology
Method used
Image
Examples
Embodiment 1
[0047] Crush the thermosetting waste plastics, use a standard sieve to sieve out the particles with the required mesh size of 60 mesh, and then fully stir and mix them with the catalytic cracking oil slurry. The mixing ratio of thermosetting waste plastics and industrial by-product heavy oil is 1:1. Take 500g of the mixture, put it into the still, set the temperature rise rate of the reaction vessel to 1°C / min, fill it with inert gas, and start vacuum distillation after emptying, the temperature of the distillation cut fraction is 450°C, and the temperature in the still is 350°C ℃. After the distillation is over, take out the distillation residue asphalt, put it into the carbonization furnace, and set up three-stage heating: 1. In an inert atmosphere, heat up from room temperature to 500°C, with a heating rate of 10°C / min, stay for 5 hours, and naturally cool to room temperature ;2. In air atmosphere, heat up from room temperature to 310°C at a heating rate of 1°C / min, stay fo...
Embodiment 2
[0049] Crush thermosetting waste plastics, use a standard sieve to sieve out the required mesh particles of 100 meshes, and then fully stir and mix them with coal tar. The mixing ratio of thermosetting waste plastics and industrial by-product heavy oil is 1:3. Take 500g of the mixed material, put it into the still, set the temperature rise rate of the reaction vessel to 5°C / min, fill it with inert gas, and start vacuum distillation after emptying, the temperature of the distillation cut fraction is 500°C, and the temperature in the still is 300°C ℃. After the distillation is over, take out the distillation residue asphalt, put it into the carbonization furnace, and set three-stage heating: 1. In an inert atmosphere, the temperature is raised from room temperature to 450°C, and the heating rate is 8°C / min, and it stays for 5 hours, and then naturally cools to room temperature. ;2. In air atmosphere, heat up from room temperature to 280°C at a heating rate of 1°C / min, stay for 2...
Embodiment 3
[0051] Crush the thermosetting waste plastics, use a standard sieve to sieve the particles with the required mesh size of 80 mesh, and then fully stir and mix them with pharmaceutical residues. The mixing ratio of thermosetting waste plastics and industrial by-product heavy oil is 1:2. Take 500g of the mixture, put it into the still, set the temperature rise rate of the reaction vessel to 1°C / min, fill it with inert gas, and start vacuum distillation after emptying, the temperature of the distillation cut fraction is 450°C, and the temperature in the still is 350°C ℃. After the distillation is over, take out the distillation residue asphalt, put it into the carbonization furnace, and set the three-stage heating program: 1. In an inert atmosphere, the temperature is raised from room temperature to 480°C, the heating rate is 5°C / min, and it stays for 6h, then naturally cools down to room temperature ;2. Raise the temperature from room temperature to 350°C in an air atmosphere at...
PUM
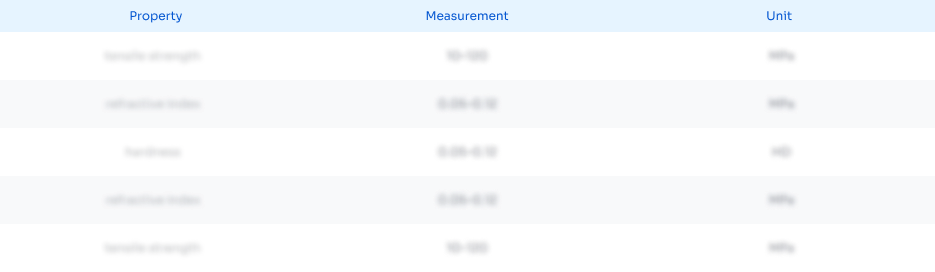
Abstract
Description
Claims
Application Information

- R&D Engineer
- R&D Manager
- IP Professional
- Industry Leading Data Capabilities
- Powerful AI technology
- Patent DNA Extraction
Browse by: Latest US Patents, China's latest patents, Technical Efficacy Thesaurus, Application Domain, Technology Topic, Popular Technical Reports.
© 2024 PatSnap. All rights reserved.Legal|Privacy policy|Modern Slavery Act Transparency Statement|Sitemap|About US| Contact US: help@patsnap.com