Composite phase change flat plate heat pipe for satellite
A flat heat pipe and composite technology, applied in the field of thermal management, can solve problems such as low thermal conductivity, affecting energy storage rate, and large temperature difference
- Summary
- Abstract
- Description
- Claims
- Application Information
AI Technical Summary
Problems solved by technology
Method used
Image
Examples
Embodiment 1
[0036] Embodiment 1: This embodiment is in the shape of a flat cube with a specific size of 280mm×280mm×20mm, and the interior is divided into a temperature uniform layer and a phase change layer.
[0037] The uniform temperature layer is in the shape of a flat square, with a specific size of 280mm×280mm×10mm, the wall thickness of the cover plate 1 and the bottom are both 3mm, and the depth of the inner cavity is 4mm. The uniform temperature layer uses a matrix of supporting ribs 6 to strengthen the mechanical properties. The supporting ribs 6 are square. The size of each supporting rib 6 is 6mm×6mm, the height is 4mm, and the spacing is 14mm. The material used is aluminum.
[0038] The phase change layer is in the shape of a flat square, with a specific size of 280mm×280mm×10mm and a wall thickness of 3mm. The upper wall is the bottom surface of the temperature uniform layer, which is welded as a whole by diffusion welding. The phase change layer strengthens the heat exchan...
PUM
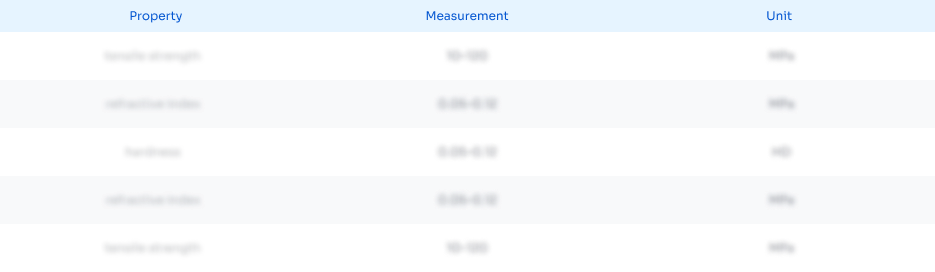
Abstract
Description
Claims
Application Information

- Generate Ideas
- Intellectual Property
- Life Sciences
- Materials
- Tech Scout
- Unparalleled Data Quality
- Higher Quality Content
- 60% Fewer Hallucinations
Browse by: Latest US Patents, China's latest patents, Technical Efficacy Thesaurus, Application Domain, Technology Topic, Popular Technical Reports.
© 2025 PatSnap. All rights reserved.Legal|Privacy policy|Modern Slavery Act Transparency Statement|Sitemap|About US| Contact US: help@patsnap.com