Photoresist pigment color paste and preparation method thereof
A technology for pigment paste and photoresist, which is applied in pigment paste, photosensitive materials for opto-mechanical equipment, etc., and can solve problems such as uneven dispersion of pigments
- Summary
- Abstract
- Description
- Claims
- Application Information
AI Technical Summary
Problems solved by technology
Method used
Examples
Embodiment 1
[0032] A kind of photoresist pigment paste, by weight, mainly comprises: 10 parts of acrylic resin, 30 parts of pretreatment pigment, 5 parts of wetting and dispersing agent, 60 parts of propylene glycol methyl ether acetate and 5 parts of n-butyl acetate .
[0033] A preparation method of photoresist pigment paste, the preparation method of said photoresist pigment paste mainly comprises the following preparation steps:
[0034] (1) Mix the graphene oxide aqueous solution with a mass fraction of 3% and N,N-dimethylformamide at a mass ratio of 1:1, and then enter the cyclone separator together with nitrogen gas heated to 130°C for spray drying , to obtain a modified graphene blank;
[0035] (2) Put the modified graphene blank obtained in step (1) into the calciner, and pass nitrogen into the calciner, heat and reduce it at a temperature of 800 ° C for 2 hours, cool to room temperature and discharge to obtain the modified Graphene;
[0036] (3) After heating and melting the pa...
Embodiment 2
[0044] A kind of photoresist pigment paste, by weight, mainly comprises: 10 parts of acrylic resin, 30 parts of pretreatment pigment, 5 parts of wetting and dispersing agent, 60 parts of propylene glycol methyl ether acetate and 5 parts of n-butyl acetate .
[0045] A preparation method of photoresist pigment paste, the preparation method of said photoresist pigment paste mainly comprises the following preparation steps:
[0046] (1) After heating and melting the paraffin, and mixing it with an initiator 0.01 times the mass of the paraffin to obtain a paraffin mixture, mix the paraffin mixture and styrene in a flask at a mass ratio of 5:2, inject nitrogen gas into the flask, and After stirring and reacting at a temperature of 95°C for 3 hours, the pretreated paraffin was obtained. The mixed dispersion of the pretreated paraffin and maleic anhydride was mixed in a three-necked flask at a mass ratio of 2:1, and the temperature was 60°C in an air atmosphere. Stir and react under...
Embodiment 3
[0054] A kind of photoresist pigment paste, by weight, mainly comprises: 10 parts of acrylic resin, 30 parts of pretreatment pigment, 5 parts of wetting and dispersing agent, 60 parts of propylene glycol methyl ether acetate and 5 parts of n-butyl acetate .
[0055] A preparation method of photoresist pigment paste, the preparation method of said photoresist pigment paste mainly comprises the following preparation steps:
[0056] (1) After mixing the graphene oxide aqueous solution with a mass fraction of 3% and N,N-dimethylformamide at a mass ratio of 1:1, it enters a cyclone separator together with nitrogen gas heated to 130°C for spray drying , to obtain a modified graphene blank;
[0057] (2) Put the modified graphene blank obtained in step (1) into the calciner, and pass nitrogen gas into the calciner, heat and reduce it at a temperature of 800°C for 2 hours, then cool to room temperature and discharge to obtain the modified Graphene;
[0058] (3) After heating and mel...
PUM
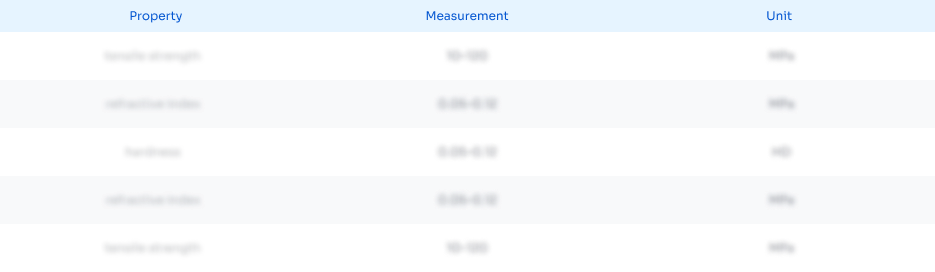
Abstract
Description
Claims
Application Information

- R&D
- Intellectual Property
- Life Sciences
- Materials
- Tech Scout
- Unparalleled Data Quality
- Higher Quality Content
- 60% Fewer Hallucinations
Browse by: Latest US Patents, China's latest patents, Technical Efficacy Thesaurus, Application Domain, Technology Topic, Popular Technical Reports.
© 2025 PatSnap. All rights reserved.Legal|Privacy policy|Modern Slavery Act Transparency Statement|Sitemap|About US| Contact US: help@patsnap.com