Production process of concrete additive
A production process and additive technology, applied in the field of production technology of concrete additives, can solve the problems of inconvenient concrete impermeability, improve concrete fluidity, inconvenient access to raw materials, etc. Waterproof effect
- Summary
- Abstract
- Description
- Claims
- Application Information
AI Technical Summary
Problems solved by technology
Method used
Image
Examples
Embodiment 1
[0034] see figure 1 , the present invention provides a technical solution: a production process for concrete additives, comprising the following steps:
[0035] S1. Raw material preparation: select raw materials according to the following parts by weight, 5 parts of magnesium silicate, 10 parts of modified cement, 5 parts of fly ash, 8 parts of ore powder, 6 parts of soil, 18 parts of quartz sand, KH550 silane coupling agent 0.5 parts, 4 parts of acrylic acid, 14 parts of ethylene-vinyl acetate copolymer, 1 part of fiber, 5 parts of superplasticizer, 1 part of reinforcing agent, 0.4 part of crosslinking agent, 0.5 part of free radical initiator, 0.2 part of antioxidant , 0.1 part of compound waterproof agent, 1 part of ferric oxide and 0.2 part of ultraviolet absorber;
[0036] S2. Prepare modified inorganic filler powder: take magnesium silicate, modified cement, fly ash, ore powder, soil, quartz sand and KH550 silane coupling agent by weight, put them into the mixer, and he...
Embodiment 2
[0056] see figure 1 , the present invention provides a technical solution: a production process for concrete additives, comprising the following steps:
[0057] S1. Raw material preparation: select raw materials according to the following parts by weight, 18 parts of magnesium silicate, 20 parts of modified cement, 18 parts of fly ash, 30 parts of ore powder, 20 parts of soil, 42 parts of quartz sand, KH550 silane coupling agent 3 parts, 16 parts of acrylic acid, 50 parts of ethylene-vinyl acetate copolymer, 4 parts of fiber, 12 parts of superplasticizer, 4 parts of reinforcing agent, 2.4 parts of crosslinking agent, 3.6 parts of free radical initiator, 1.4 parts of antioxidant , 1.2 parts of compound waterproofing agent, 3 parts of ferric oxide and 0.6 parts of ultraviolet absorber;
[0058] S2. Prepare modified inorganic filler powder: take magnesium silicate, modified cement, fly ash, ore powder, soil, quartz sand and KH550 silane coupling agent by weight, put them into th...
Embodiment 3
[0078] see figure 1 , the present invention provides a technical solution: a production process for concrete additives, comprising the following steps:
[0079] S1. Raw material preparation: select raw materials according to the following parts by weight, 12 parts of magnesium silicate, 15 parts of modified cement, 12 parts of fly ash, 15 parts of ore powder, 15 parts of soil, 24 parts of quartz sand, KH550 silane coupling agent 2 parts, 8 parts of acrylic acid, 30 parts of ethylene-vinyl acetate copolymer, 2 parts of fiber, 8 parts of superplasticizer, 2 parts of reinforcing agent, 1 part of crosslinking agent, 3 parts of free radical initiator, 1 part of antioxidant , 0.5 parts of compound waterproofing agent, 2 parts of ferric oxide and 0.4 parts of ultraviolet absorber;
[0080] S2. Prepare modified inorganic filler powder: take magnesium silicate, modified cement, fly ash, ore powder, soil, quartz sand and KH550 silane coupling agent by weight, put them into the mixer, a...
PUM
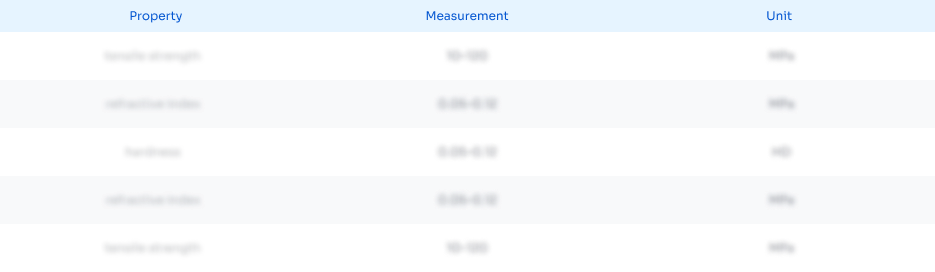
Abstract
Description
Claims
Application Information

- R&D Engineer
- R&D Manager
- IP Professional
- Industry Leading Data Capabilities
- Powerful AI technology
- Patent DNA Extraction
Browse by: Latest US Patents, China's latest patents, Technical Efficacy Thesaurus, Application Domain, Technology Topic, Popular Technical Reports.
© 2024 PatSnap. All rights reserved.Legal|Privacy policy|Modern Slavery Act Transparency Statement|Sitemap|About US| Contact US: help@patsnap.com