Oxygen jet multi-stage dispersion combustion roaster
A dispersion combustion and roaster technology, which is applied to gas fuel burners, burners, combustion methods, etc., can solve problems such as airflow short circuit, complex equipment structure, blockage and crushing of regenerators, etc., to reduce the temperature difference between the upper and lower sides and improve Baking efficiency, heat loss reduction effect
- Summary
- Abstract
- Description
- Claims
- Application Information
AI Technical Summary
Problems solved by technology
Method used
Image
Examples
Embodiment 1
[0026] A 100-ton ladle uses coke oven gas as fuel and uses an oxygen jet multi-stage diffuse combustion roaster. After the ladle is transported back from the continuous casting empty ladle, it needs to be baked. First, turn on the secondary combustion air and primary gas in the center. After the flame is stable, turn on the primary compressed air in the center, and finally turn on the secondary gas and the tertiary oxygen in the outer ring. After baking for 24 minutes, the temperature reaches 1080°C. After the baking is over, it is sent to the converter to wait for steel connection. Gas consumption from the original 585Nm 3 / h reduced to 320Nm 3 / h, the fuel saving rate is 45.3%.
Embodiment 2
[0028] A 200-ton ladle uses mixed gas as fuel and uses an oxygen jet multi-stage diffuse combustion roaster. After the ladle is transported back from the continuous casting empty ladle, it needs to be baked. First, the secondary combustion air and primary gas in the center are turned on. After baking for 38 minutes, it reaches 1109°C. After the baking is over, it is sent to the converter to wait for steel connection. Gas consumption from the original 1806Nm 3 / h reduced to 929m 3 / h, saving 48.6% of gas.
Embodiment 3
[0030] A 200-ton ladle uses converter gas as fuel and uses an oxygen jet multi-stage diffuse combustion roaster. After the ladle is transported back from the continuous casting empty ladle, it needs to be baked. First, the secondary combustion air and primary gas in the center are turned on. After baking for 32 minutes, it reaches 1077°C, and the baking is over, and it is sent to the converter to wait for steel connection. Gas consumption from the original 3679Nm 3 / h reduced to 1648m 3 / h, saving 55.2% of gas.
PUM
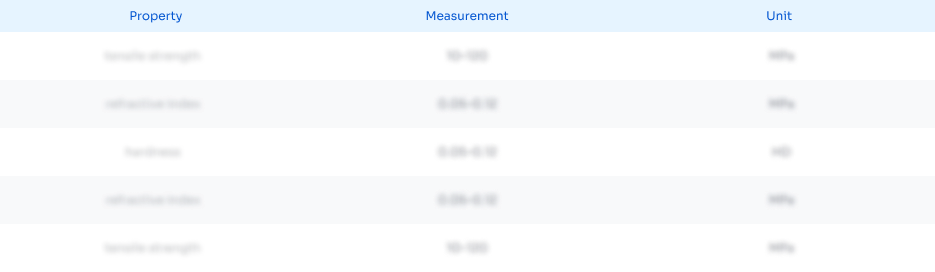
Abstract
Description
Claims
Application Information

- R&D Engineer
- R&D Manager
- IP Professional
- Industry Leading Data Capabilities
- Powerful AI technology
- Patent DNA Extraction
Browse by: Latest US Patents, China's latest patents, Technical Efficacy Thesaurus, Application Domain, Technology Topic, Popular Technical Reports.
© 2024 PatSnap. All rights reserved.Legal|Privacy policy|Modern Slavery Act Transparency Statement|Sitemap|About US| Contact US: help@patsnap.com