Method for preparing plastic filler by taking gasified slag as raw material
A technology for gasification slag and coal gasification slag, which is applied in chemical instruments and methods, magnetic separation, solid separation, etc., can solve the problems of difficult to achieve industrialization, unstable composition of gasification slag, and low dosage, and achieves modification. The effect of improving the effect and crushing efficiency, saving natural mineral resources, and shortening the process flow
- Summary
- Abstract
- Description
- Claims
- Application Information
AI Technical Summary
Problems solved by technology
Method used
Image
Examples
Embodiment 1
[0039] see figure 1 , a method for preparing plastic filler with gasification slag as raw material, has the following steps:
[0040] (1) Raw material pretreatment
[0041] The coal gasification slag is directly treated or the coal gasification slag is prepared into a slurry for treatment. The raw material pretreatment process includes a decarbonization stage, a magnetic separation stage and a dehydration stage; the decarburization is determined according to the actual carbon content in the coal gasification slag Whether the stage is carried out, the decarbonization stage is to use the flotation process or gravity separation process to remove the carbon part of the coal gasification slag. When the carbon content in the coal gasification slag raw material is greater than 5%, it will cause the oil absorption value of subsequent products to be too large , affecting the processing performance of subsequent products, it is necessary to decarburize the coal gasification slag. When ...
Embodiment 2
[0047] combine figure 1 Embodiment 1 is further described and explained in detail. The decarbonization stage, magnetic separation stage, and dehydration stage are freely adjusted and combined according to the content of each component in the coal gasification slag to realize the raw material pretreatment process;
[0048] When the flotation process is adopted in the decarbonization stage, kerosene or light diesel oil is used as a collector, 2-octanol or No. 2 oil is used as a foaming agent, and water circulation is used for flotation; the amount of the foaming agent is 0.005-0.1% of the total amount of slag, and the amount of the collector is 0.02-0.5% of the total amount of coal gasification slag;
[0049] The magnetic separation stage removes various heavy metals such as iron oxide, titanium oxide, manganese oxide, and chromium oxide in the coal gasification slag, and the magnetic field strength of the magnetic separator in the magnetic separation stage is adjustable within ...
Embodiment 3
[0056] In the coal gasification slag produced in the production process of a company, the residual carbon content is 15.3%, the iron oxide content is 3.6%, the manganese oxide content is not detected, and the moisture content is 4%. Flash drying, magnetic separation to remove iron.
[0057] Firstly, the coal gasification slag was made into a slurry with a concentration of 30%, with 0.1% kerosene as a collector and 0.05% 2-octanol as a detonator, and flotation three times; using a wet magnetic separator in a 1.5T Magnetic separation under high intensity once; after concentrating the slurry, use a filter press to dehydrate to a water content of 15%; use flash drying equipment to dry the coal gasification slag after flotation under the conditions of an inlet temperature of 200°C and an outlet temperature of 100°C Then the dried material is fed into the steam kinetic energy mill with a screw feeder, using superheated steam at 0.7MPa and 290°C, the speed of the classifier is 1500rp...
PUM
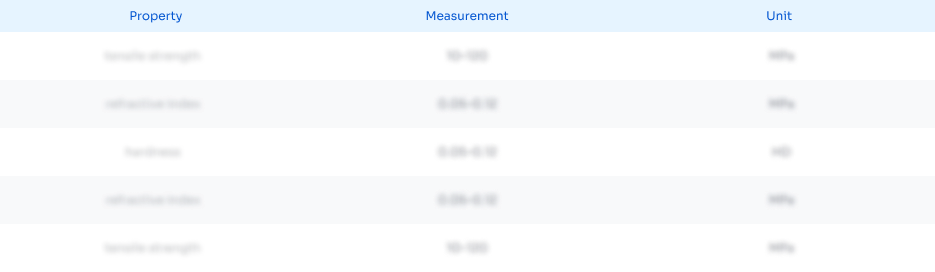
Abstract
Description
Claims
Application Information

- Generate Ideas
- Intellectual Property
- Life Sciences
- Materials
- Tech Scout
- Unparalleled Data Quality
- Higher Quality Content
- 60% Fewer Hallucinations
Browse by: Latest US Patents, China's latest patents, Technical Efficacy Thesaurus, Application Domain, Technology Topic, Popular Technical Reports.
© 2025 PatSnap. All rights reserved.Legal|Privacy policy|Modern Slavery Act Transparency Statement|Sitemap|About US| Contact US: help@patsnap.com