RTO treatment process for tail gas produced by ammoxidation process
A treatment process and ammonia oxidation technology, applied in the field of environmental engineering, can solve the problems of high cost, unstable operation, low efficiency, etc., and achieve the effects of high thermal energy utilization rate, high operation stability, and high removal efficiency.
- Summary
- Abstract
- Description
- Claims
- Application Information
AI Technical Summary
Problems solved by technology
Method used
Image
Examples
Embodiment 1
[0033] Ammonia oxidation tail gas source strength: ammonia 3800mg / m 3 , Hydrogen cyanide 300mg / m 3 , Nitrile organic substance 320mg / m 3 , Benzene 300mg / m 3 .
[0034]High concentration (organized) exhaust gas and low concentration (no tissue) exhaust gas mixed exhaust gas temperature at 140 ° C, the temperature of the exhaust gas in the exhaust gas heating mix tank is 180 ° C, the RTO combustion chamber temperature is 880 ° C, flue gas mix The exhaust gas temperature after mixing the box is 300 ° C. SCR catalyst specific surface area 900m 2 / m 3 , Urea solution concentration is 5% wt, the spray density of the washing tower is 4m 3 / (m 2 , H), the base concentration of the base is 5% wt.
[0035] Ammonia ≤22mg / m after treatment 3 , Hydrogen cyanide ≤0.02mg / m 3 , Nitrile organic matter ≤ 2mg / m 3 , Benzene ≤ 1mg / m 3 , NOx ≤ 70mg / m 3 , Emissions stably meet the national and local emissions standards and requirements.
Embodiment 2
[0037] Ammonia oxidation exhaust source strength: ammonia 720mg / m 3 , Hydrogen cyanide 1700mg / m 3 , Nitrile organic matter 150mg / m 3 , Benzene 110mg / m 3 .
[0038] High concentration (organized) exhaust gas and low concentration (no tissue) exhaust gas mixed exhaust gas temperature at 160 ° C, the temperature of the exhaust gas in the exhaust gas heating mix tank is 200 ° C, the RTO combustion chamber temperature is 880 ° C, flue gas mix The exhaust gas temperature after the mixture is 320 ° C. SCR catalyst specific surface area 1100m 2 / m 3 , Urea solution concentration is 5% wt, the spray density of the washing tower is 3m 3 / (m 2 , H), the use of the base concentration of 10% wt.
[0039] Ammonia ≤13mg / m after treatment 3 , Hydrogen cyanide ≤0.08mg / m 3 , Nitrile organic matter ≤1.3mg / m 3 , Benzene ≤0.8mg / m 3 NOx ≤ 50mg / m 3 , Emissions stably meet the national and local emissions standards and requirements.
Embodiment 3
[0041] Ammonia oxidation tail gas source strength: ammonia 220mg / m 3 , Hydrogen cyanide 900mg / m 3 , Nitrile organic substances 80mg / m 3 , Benzene material 130mg / m 3 .
[0042] High concentration (organized) exhaust gas and low concentration (no tissue) exhaust gas mixed exhaust gas temperature at 160 ° C, the temperature of the exhaust gas in the exhaust gas heating mix tank is 200 ° C, the RTO combustion chamber temperature is 850 ° C, flue gas mix The exhaust gas temperature after mixing the box is 300 ° C. SCR catalyst specific surface area 1100m 2 / m 3 , The urea solution concentration is 8% wt, the spray density of the washing tower is 3m 3 / (m 2 , H), the use of the base concentration of 10% wt.
[0043] Ammonia ≤12mg / m after treatment 3 , Hydrogen cyanide ≤0.06mg / m 3 , Nitrile organic matter ≤1.9mg / m 3 , Benzene ≤ 2.8mg / m 3 NOx ≤ 40mg / m 3 , Emissions stably meet the national and local emissions standards and requirements.
PUM
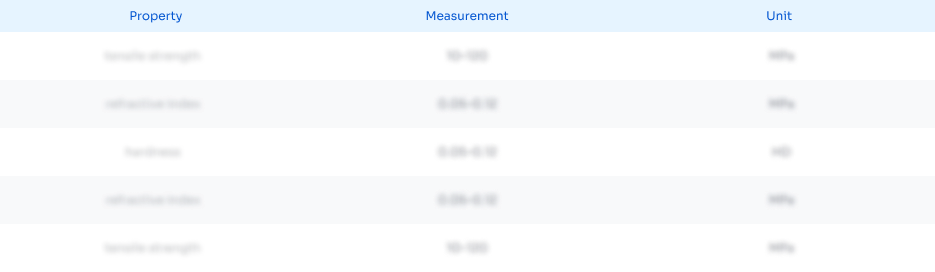
Abstract
Description
Claims
Application Information

- R&D Engineer
- R&D Manager
- IP Professional
- Industry Leading Data Capabilities
- Powerful AI technology
- Patent DNA Extraction
Browse by: Latest US Patents, China's latest patents, Technical Efficacy Thesaurus, Application Domain, Technology Topic, Popular Technical Reports.
© 2024 PatSnap. All rights reserved.Legal|Privacy policy|Modern Slavery Act Transparency Statement|Sitemap|About US| Contact US: help@patsnap.com