Additive manufacturing workpiece forming quality monitoring and predicting method based on deep learning
A forming quality, additive manufacturing technology, applied in computer parts, instruments, data processing applications, etc., can solve the problem of unstable repeatability of the additive manufacturing process, inability to guarantee the forming quality of parts, and inability to predict the forming quality of parts and other problems to achieve the effect of improving repeatability, reducing processing time, and improving the quality of parts
- Summary
- Abstract
- Description
- Claims
- Application Information
AI Technical Summary
Problems solved by technology
Method used
Image
Examples
Embodiment Construction
[0025] In order to make the object, technical solution and advantages of the present invention clearer, the present invention will be further described in detail below in conjunction with the accompanying drawings.
[0026] like figure 1 , figure 2 As shown, the implementation carrier structure of the present invention includes a laser transmitter 1, an optical fiber interface 2, a high-speed camera and an infrared (Infrared) camera combination module 3, a laser cladding head 4, a powder feeding channel 5, a molten pool 6, and a powder feeder 7. Formed parts 8 and substrate 9. During the additive manufacturing process, the high-speed camera and infrared camera combination module 3 takes real-time photos and captures the dynamic characteristics of the molten pool 6 area. Acquire geometric and temperature characteristic images of the melt pool, plume, and spatter.
[0027] combine image 3 As shown, a method for monitoring and predicting the forming quality of additively man...
PUM
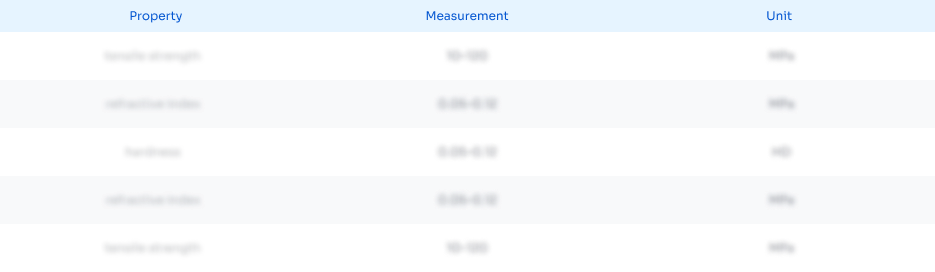
Abstract
Description
Claims
Application Information

- Generate Ideas
- Intellectual Property
- Life Sciences
- Materials
- Tech Scout
- Unparalleled Data Quality
- Higher Quality Content
- 60% Fewer Hallucinations
Browse by: Latest US Patents, China's latest patents, Technical Efficacy Thesaurus, Application Domain, Technology Topic, Popular Technical Reports.
© 2025 PatSnap. All rights reserved.Legal|Privacy policy|Modern Slavery Act Transparency Statement|Sitemap|About US| Contact US: help@patsnap.com