Processing technology for enhancing thermal protection of metal piece
A processing technology and metal parts technology, which is applied in the field of processing technology to enhance the thermal protection of metal parts, can solve the problems of reducing the thermal protection efficiency of metal parts, poor contact effect of the protective layer, poor temperature resistance of the protective layer, etc.
- Summary
- Abstract
- Description
- Claims
- Application Information
AI Technical Summary
Problems solved by technology
Method used
Examples
Embodiment 1
[0025] A processing technology for enhancing the thermal protection of metal parts in this embodiment includes the following steps:
[0026] Step 1, preparation of surfactant: add 50 parts of acrylamide to a magnetic stirrer, then add 3,5-diamino-1,2,4-triazole with 20% of the total amount of acrylamide, and react The temperature rises to 95°C, the reaction time is 20min, and the reaction speed is 500r / min, then add 10 parts of modified wollastonite powder, then stir at a speed of 100- / min for 35min, and finally carry out ultrasonic dispersion with a power of 100W for 10min. Obtain surfactant;
[0027] Step 2, the surface treatment of metal parts: send the metal parts into the cold plasma box for irradiation treatment, the irradiation power is 200W, and the irradiation time is 10min, and then use 60 CO-γ-ray irradiation for 10s, the irradiation dose rate is 510Gy / h;
[0028] Step 3, activation treatment: send the surface-treated metal parts in step 2 into the surfactant in s...
Embodiment 2
[0039] A processing technology for enhancing the thermal protection of metal parts in this embodiment includes the following steps:
[0040] Step 1, preparation of surfactant: add 70 parts of acrylamide to a magnetic stirrer, then add 3,5-diamino-1,2,4-triazole with 30% of the total amount of acrylamide, and react The temperature rises to 105°C, the reaction time is 20-30min, and the reaction speed is 1000r / min, then add 20 parts of modified wollastonite powder, then stir at a speed of 500r / min for 45min, and finally carry out ultrasonic dispersion with a power of 500W for 20min , to obtain surfactant;
[0041] Step 2, the surface treatment of metal parts: send the metal parts into the cold plasma box for irradiation treatment, the irradiation power is 300W, and the irradiation time is 20min, and then adopt 60 CO-γ-ray irradiation for 20s, the irradiation dose rate is 550Gy / h;
[0042] Step 3, activation treatment: send the surface-treated metal parts in step 2 into the surf...
Embodiment 3
[0053] A processing technology for enhancing the thermal protection of metal parts in this embodiment includes the following steps:
[0054] Step 1, preparation of surfactant: add 60 parts of acrylamide to a magnetic stirrer, then add 3,5-diamino-1,2,4-triazole with 25% of the total amount of acrylamide, and react The temperature rises to 100°C, the reaction time is 25min, and the reaction speed is 750r / min, then add 15 parts of modified wollastonite powder, then stir for 40min at a speed of 300r / min, and finally carry out ultrasonic dispersion with a power of 100-500W for 15min , to obtain surfactant;
[0055] Step 2, the surface treatment of metal parts: send the metal parts into the cold plasma box for irradiation treatment, the irradiation power is 250W, and the irradiation time is 15min, then use 60 CO-γ-ray irradiation for 15s, the irradiation dose rate is 530Gy / h;
[0056] Step 3, activation treatment: send the surface-treated metal parts in step 2 into the surfactant...
PUM
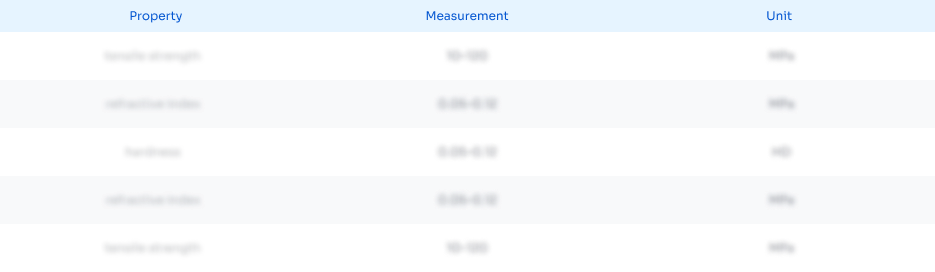
Abstract
Description
Claims
Application Information

- R&D
- Intellectual Property
- Life Sciences
- Materials
- Tech Scout
- Unparalleled Data Quality
- Higher Quality Content
- 60% Fewer Hallucinations
Browse by: Latest US Patents, China's latest patents, Technical Efficacy Thesaurus, Application Domain, Technology Topic, Popular Technical Reports.
© 2025 PatSnap. All rights reserved.Legal|Privacy policy|Modern Slavery Act Transparency Statement|Sitemap|About US| Contact US: help@patsnap.com