Method for eliminating chlorine-containing volatile organic pollutants through high-temperature catalytic combustion
A volatile organic compound and volatile organic technology is applied in the field of high-temperature catalytic combustion and elimination of chlorine-containing volatile organic pollutants, and can solve the problems of many chlorine-containing by-products, deactivation, and easy carbon deposition.
- Summary
- Abstract
- Description
- Claims
- Application Information
AI Technical Summary
Problems solved by technology
Method used
Examples
Embodiment 1
[0016] Preparation of hexaaluminate LaM by coprecipitation method x al 12-x o 19 (M=Fe, Co, Ce, Cu, Ni, Mn) catalyst materials, prepare metal nitrate mixed solution and ammonium carbonate solution according to the stoichiometric ratio of the target product. At 60°C, pour the mixed cation solution into the saturated ammonium carbonate solution, and maintain the Ph at about 7.5-9.0. After aging with stirring for 3 hours, it was centrifuged and dried at 120°C for 12 hours. After the dried sample was ground, it was placed in a corundum crucible, the temperature was raised to 500°C at 5°C / min, and maintained for 5 hours, and then the temperature was raised from 500°C to 1200°C at 2°C / min for 6 hours.
[0017] In the air reaction atmosphere, hexaaluminate LaMn 3 al 9 o 19The catalyst is used for the catalytic degradation of 1,2-dichloroethane. The evaluation of reaction performance was carried out in a fixed-bed continuous flow reactor, and 1,2-dichloroethane gas was a custom...
Embodiment 2
[0019] Adopt the method for embodiment 1 to prepare hexaaluminate LaFeAl 11 o 19 Catalyst for the catalytic degradation of dichlorobenzene. In an air reaction atmosphere, the hexaaluminate LaFeAl 11 o 19 The catalyst is used for the catalytic degradation of dichlorobenzene. The reaction evaluation method is the same as in Example 1, carried out in a fixed-bed continuous flow device, o-dichlorobenzene gas generates steam by bubbling at a specific temperature, the o-dichlorobenzene concentration is 500 ppm, and the total flow of gas is 400 ml / min, the concentration of water is 4000 ppm, and the reaction temperature is 200-1000°C. The results showed that under the air reaction atmosphere, 500 ppm of dichlorobenzene was completely degraded at 500℃, and no organic and chlorinated organic by-products were formed at this temperature. After operating at 500°C, 800°C and 1000°C for 100 hours, the removal rate of p-dichlorobenzene was 100%, and no organic by-products were detected ...
Embodiment 3
[0021] Preparation of hexaaluminate LaM by sol-gel method x Al 12-x o 19 (M=Fe, Co, Ce, Cu, Ni, Mn) catalyst material. According to the stoichiometric ratio of the target product, the metal nitrate mixture and La(NO 3 ) 3 ∙6H 2 The O solution is mixed, and an appropriate amount of aminoacetic acid is added (to meet the molar ratio COOH / NO 3- =1.05,), heated and stirred in a constant temperature water bath at 8090 °C to evaporate to gel, pre-decomposed at 250 °C for 30 min, put the decomposed precursor in a muffle furnace and roasted at 1200 °C for 5 h, cooled, pressed into tablets and sieved into 4080 mesh granular catalyst.
[0022] The prepared hexaaluminate LaCu 3 Al 9 o 19 The catalyst is used for the catalytic degradation of 1,2-dichloroethane. The evaluation method of the reaction performance is basically the same as that of Example 1, except that the concentration of 1,2-dichloroethane to be treated is 20000 ppm. The results showed that 20,000 ppm of 1,2-dich...
PUM
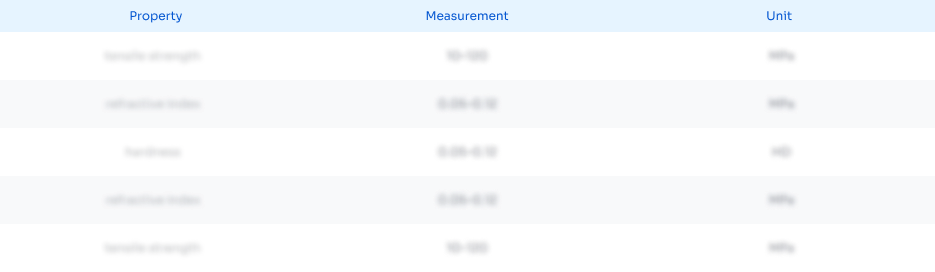
Abstract
Description
Claims
Application Information

- R&D
- Intellectual Property
- Life Sciences
- Materials
- Tech Scout
- Unparalleled Data Quality
- Higher Quality Content
- 60% Fewer Hallucinations
Browse by: Latest US Patents, China's latest patents, Technical Efficacy Thesaurus, Application Domain, Technology Topic, Popular Technical Reports.
© 2025 PatSnap. All rights reserved.Legal|Privacy policy|Modern Slavery Act Transparency Statement|Sitemap|About US| Contact US: help@patsnap.com