Carbon fiber composite material arm joint and preparation method thereof
A composite material and carbon fiber technology, applied in the processing of building materials, construction, building structure, etc., can solve the problems of unreasonable force transmission design, general surface quality control, insufficient strength of connecting parts, etc. Strength and fatigue properties, the effect of ensuring the strength of the interface connection, improving the overall mechanical performance and long-term reliability
- Summary
- Abstract
- Description
- Claims
- Application Information
AI Technical Summary
Problems solved by technology
Method used
Image
Examples
Embodiment 1
[0058] Such as figure 1 , 2 , 3, 4, and 5, a carbon fiber composite arm section in this embodiment includes: a carbon fiber composite shell 1, an inner core 2, a large end connection embedded part 3, a small end connection pre-embedded Embedded part 4, conveying pipe support embedded part 5. The inner core 2 is filled in the interior of the carbon fiber composite material shell 1; the big end end connection embedded part 3 is arranged at the big end of the carbon fiber composite material shell 1, and is embedded in the inner core for The connection between the large end of the carbon fiber composite boom section and another boom section or hydraulic device; the small end connection embedded part 4 is set at the small end of the carbon fiber composite material shell 1 and embedded in the inner core 2 Among them, it is used to connect the small end of the carbon fiber composite material arm section with another arm section or hydraulic device; the conveying pipe support embedd...
Embodiment 2
[0085] The preparation method of the carbon fiber composite arm section described in this example, the preparation steps and the size of the arm section are the same as those in Example 1, the difference is that the autoclave molding process is used for molding in step S4, and the resin transfer is used in step S5 The molding process is the RTM process for molding.
PUM
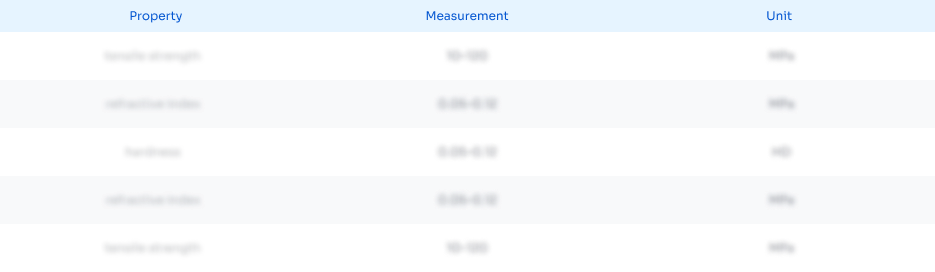
Abstract
Description
Claims
Application Information

- R&D
- Intellectual Property
- Life Sciences
- Materials
- Tech Scout
- Unparalleled Data Quality
- Higher Quality Content
- 60% Fewer Hallucinations
Browse by: Latest US Patents, China's latest patents, Technical Efficacy Thesaurus, Application Domain, Technology Topic, Popular Technical Reports.
© 2025 PatSnap. All rights reserved.Legal|Privacy policy|Modern Slavery Act Transparency Statement|Sitemap|About US| Contact US: help@patsnap.com