Device and method for high-throughput preparation of spherical powder based on laser-coaxial powder feeding coupling
A spherical powder, coaxial powder feeding technology, applied in the direction of transportation and packaging, metal processing equipment, etc., to achieve the effect of expanding the scope of application
- Summary
- Abstract
- Description
- Claims
- Application Information
AI Technical Summary
Problems solved by technology
Method used
Image
Examples
Embodiment 1
[0044] Example 1: High Throughput Powder Alloying
[0045] combine image 3 Shown, the method for preparing spherical powder based on laser-coaxial powder feeding coupling high throughput of the present invention comprises the following steps:
[0046] 1) Raw material preparation (step S101), put the powders of raw materials A, B, C, etc. with different components into the multi-channel powder feeder 1 that is isolated from each other. Such as figure 1 As shown, the ratio of different powders can be controlled by controlling the flow rate of the multi-channel powder feeder 1 through the computer system. The gas is transported to the laser spot;
[0047] 2) Powder alloying (step S102), according to the different characteristics of the raw material powder, such as melting point, wave absorption, etc., adjust the power of the laser generator to match different raw material characteristics and laser spot diameter, turn on the laser generator 2, and the raw material powder is pass...
Embodiment 2
[0050] Embodiment 2: spheroidization of flake iron-based amorphous powder
[0051] 1) Load flake FeSiCuNb powder into multi-channel powder feeder 1, its microscopic appearance is as follows Figure 2a As shown, it is an irregular flake shape, and the powder feeding rate V~20g / min is precisely controlled by the computer system, and the laser spots are transported to the bottom of the annular nozzle through the carrier gas to converge;
[0052] 2) According to the characteristics of the raw material powder, adjust the power of the laser generator 2 to match the characteristics of the raw material and the diameter of the laser spot, turn on the laser generator 2, and the raw material powder is transported to the laser spot convergence point through the multi-channel powder feeder 1. Under the action of energy, the mixed powder melts rapidly. In this embodiment, the laser power is 2000W, the rotation speed of multi-channel powder feeder 1 is 50 r / min, and the flow rate of powder ...
PUM
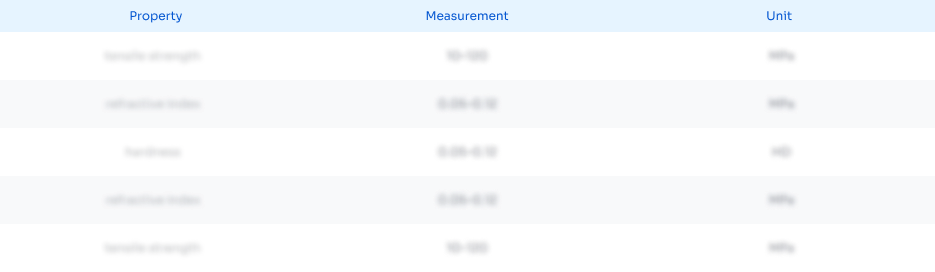
Abstract
Description
Claims
Application Information

- R&D Engineer
- R&D Manager
- IP Professional
- Industry Leading Data Capabilities
- Powerful AI technology
- Patent DNA Extraction
Browse by: Latest US Patents, China's latest patents, Technical Efficacy Thesaurus, Application Domain, Technology Topic, Popular Technical Reports.
© 2024 PatSnap. All rights reserved.Legal|Privacy policy|Modern Slavery Act Transparency Statement|Sitemap|About US| Contact US: help@patsnap.com