Secondary etching forming method for high-precision lead
A technology of secondary etching and forming method, which is applied in the direction of semiconductor devices, electrical components, circuits, etc. It can solve the problems of unable to check the tip area of the lead, affect the quality of chip bonding, and the bonding force of the metal lead is small, so as to reduce the poor lead peeling Phenomenon, reduce missed detection, good etching effect
- Summary
- Abstract
- Description
- Claims
- Application Information
AI Technical Summary
Problems solved by technology
Method used
Image
Examples
Embodiment Construction
[0033] A high-precision lead secondary etching molding method is characterized in that a metal lead 2 is designed at the corresponding position of the chip pad 1 and connected to an external circuit, the overlapping area of the chip pad 1 and the metal lead 2 is a bonding area, and the metal The tip of lead 2 exceeds the area of chip pad 1 by a certain length, including steps:
[0034] Step A: If figure 1 As shown in the design stage, the metal lead 2 is directly connected to the internal circuit of the chip position on the product or the metal leads 2 on both sides of the chip are connected to each other so that there is no breakpoint at the tip of the metal lead 2 in the circuit. In the following steps, use figure 1 The box in is a description of the zoomed-in area;
[0035] Step B: Coating a layer of photoresist 4 on the copper 3 of the product substrate, exposing the product substrate coated with photoresist 4, and using a developer to decompose the photoresist 4 at...
PUM
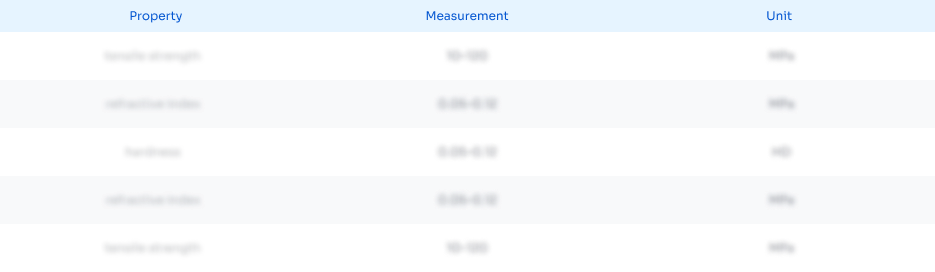
Abstract
Description
Claims
Application Information

- R&D
- Intellectual Property
- Life Sciences
- Materials
- Tech Scout
- Unparalleled Data Quality
- Higher Quality Content
- 60% Fewer Hallucinations
Browse by: Latest US Patents, China's latest patents, Technical Efficacy Thesaurus, Application Domain, Technology Topic, Popular Technical Reports.
© 2025 PatSnap. All rights reserved.Legal|Privacy policy|Modern Slavery Act Transparency Statement|Sitemap|About US| Contact US: help@patsnap.com