Method for recycling waste mineral oil
A waste mineral oil and diluent technology, applied in the petroleum industry, hydrocarbon oil treatment, hydrotreating process, etc., can solve problems such as blockage of the outlet pipeline of the hydrogenation reaction material, coking of the treatment furnace tube, corrosion of the hydrogenation equipment, etc. Achieve the effect of overcoming serious corrosion of hydrogenation equipment
- Summary
- Abstract
- Description
- Claims
- Application Information
AI Technical Summary
Problems solved by technology
Method used
Image
Examples
Embodiment 1
[0039] 1. Mix 6.25t / h of waste mineral oil after sedimentation pretreatment with a certain amount of diluent and deslagging agent, heat it to about 90°C, and deslagging by decanter centrifuge;
[0040]2. After centrifugal deslagging, the waste mineral oil is heated to about 180°C and sent to the dehydration tower for degassing and dehydration;
[0041] 3. After dehydration and degassing, the waste mineral oil is sent to a vacuum heating furnace to be heated to 320°C for vacuum fractionation in a vacuum fractionation tower, and the diluent and hydrogenation raw material are cut out, and the diluent is returned to the previous process for recycling, and the hydrogenation raw material Sent to the low-pressure hydrogenation process; the vacuum fractionation column controls the pressure to about 2.5kPa (A);
[0042] 4. After decompression cutting, the hydrogenation raw material is raised to 4.5MPa(G), and then heated to 320°C in a hydrogenation heating furnace, and then enters the ...
Embodiment 2
[0046] 1. Mix 12.5t / h of waste mineral oil after sedimentation pretreatment with a certain amount of diluent and deslagging agent, heat it to about 90°C, and deslagging by centrifuge;
[0047] 2. After centrifugal deslagging, the waste mineral oil is heated to about 180°C and sent to the dehydration tower for degassing and dehydration;
[0048] 3. After dehydration, the waste mineral oil is sent to the decompression heating furnace to be heated to 330°C, and the diluent and hydrogenation raw material are cut out. The diluent is returned to the previous process for recycling, and the hydrogenation raw material is sent to the low-pressure hydrogenation part. Vacuum fractionation column control pressure is about 2.5kPa (A);
[0049] 4. After decompression cutting, the hydrogenation raw material is raised to 5.5MPa(G), and then heated to 330°C in a low-pressure hydrogenation furnace, and then enters the protection reactor, dechlorination reactor and refining reactor respectively. ...
PUM
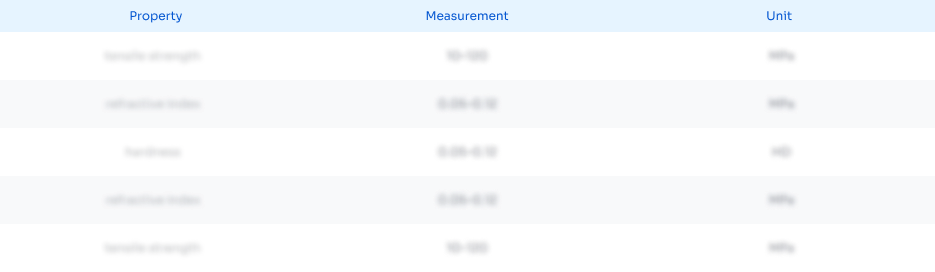
Abstract
Description
Claims
Application Information

- R&D Engineer
- R&D Manager
- IP Professional
- Industry Leading Data Capabilities
- Powerful AI technology
- Patent DNA Extraction
Browse by: Latest US Patents, China's latest patents, Technical Efficacy Thesaurus, Application Domain, Technology Topic, Popular Technical Reports.
© 2024 PatSnap. All rights reserved.Legal|Privacy policy|Modern Slavery Act Transparency Statement|Sitemap|About US| Contact US: help@patsnap.com